Few industrial processes monolithically shape the world as we know it contextually; metal fabrication is one. Every modern construction, like structural beams in skyscrapers and even small components , have fabricated metal. Despite its ubiquitous presence, many even in allied industries fail to understand the nuances behind metal fabrication.
This guide intends to inform readers about metal fabrication and everything it encompasses, from fundamental techniques to essential infrastructure. If you are a curious construction professional or someone interested in learning about the discipline, this article will be of value to you.
What is Metal Fabrication?
Definition and Core Concepts
As the name suggests, metal fabrication is the construction of distinct components by altering raw metals, be it cutting, bending, shaping, assembling, or even finishing them. Unlike mass-scale production, metal manufacturing focuses on creating custom components that cater to specific requirements.
In simple terms, metal fabrication is merging engineering and skilled handiwork to convert metal sheets, rods, and other industrial materials into usable parts or intricate structures. The welding association reports that the U.S. metal fabrication sector alone has over 400,000 skilled workers and is worth over $21 billion annually.
Maria Rodriguez, chief engineer at Advanced Fabrication Solutions, states: "As with any other field, metal fabrication embodies the blend of modern engineering and traditional craftsmanship. It’s an art as much as it is a science, for it requires in depth knowledge of the material, and skillful technique to turn raw metal into an engineered part.”
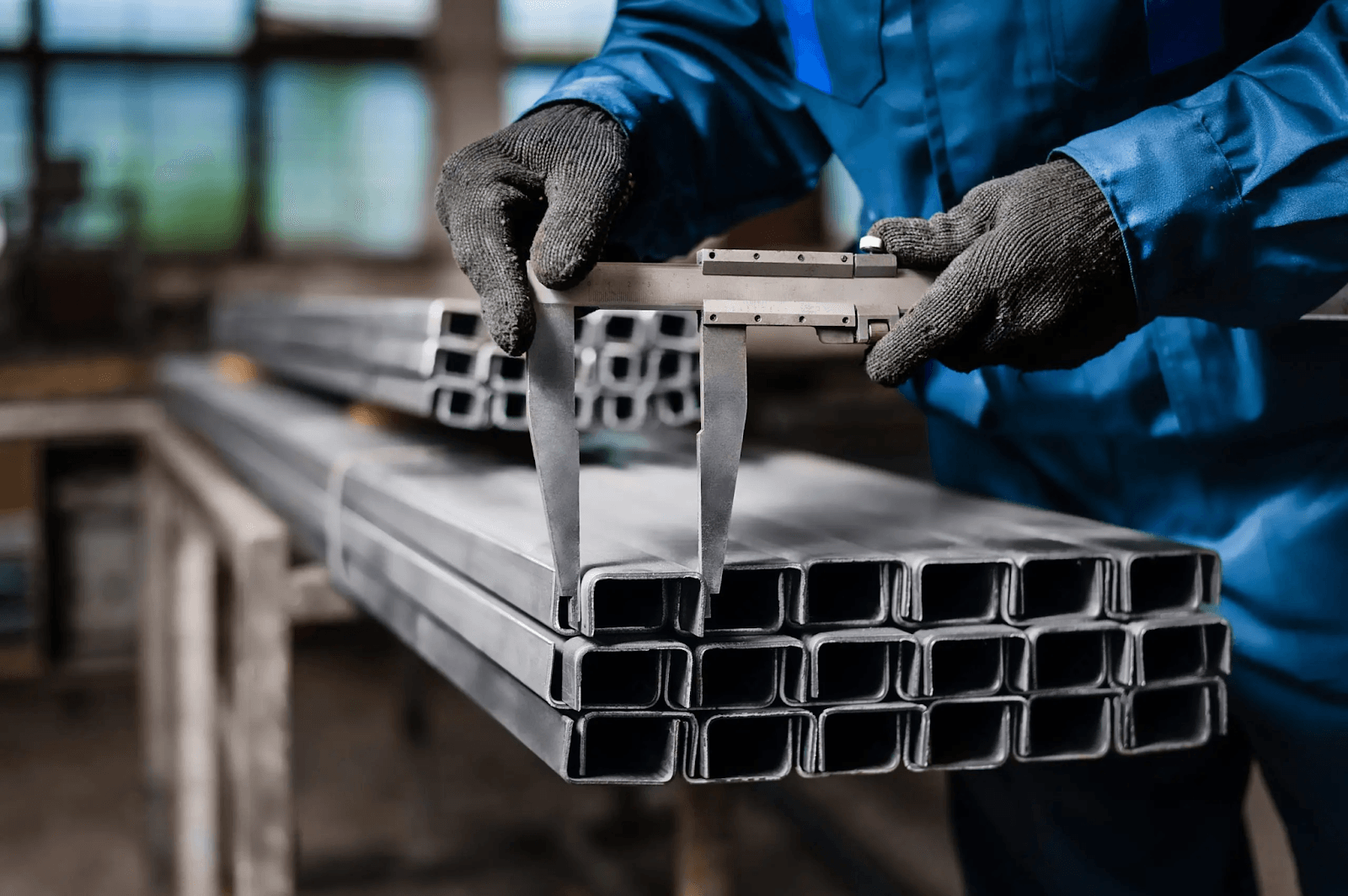
Historical Overview and Evolution
Ancient civilizations mastered a wide range of techniques, including metal fabrication. Bronze and copper metalworking can be traced back to approximately 5000 BCE. However, current practices of metal fabrication emerged during the Industrial Revolution when newly developed machinery, along with more advanced techniques, enabled more efficient and precise workings on metal.
The following is a list of some major events that have resulted in the evolution of metal fabrication:
Industrial rolling mills and presses were introduced in the 1800s.
The early relatives of arc welding techniques were developed in the early 1900s.
Basic mechanical fabrication processes were automated by the mid-twentieth century.
Computer numerical control (CNC) technology was introduced in the 1980s to the 1990s.
Robotics, digital design, and modern materials were integrated in the following decades (2000-present).
With CNC machines and robotics, advanced metal fabrication today involves traditional techniques integrated with modern technology. As much as new demands are increasingly complex and sophisticated, innovative approaches are carefully blended with traditional methods.
Metal Fabrication Processes Overview
The cutting, welding, and machining procedures.
Every metal fabrication project begins with the following three procedures:
Modern British English employs the term ‘cutting’ to denote metal breaking into specific shapes required. Today, cutting processes include:
Cutting involves separating metal into desired shapes and sizes. Modern cutting techniques include:
Laser cutting (precision cuts with minimal material waste)
Plasma cutting (effective for thicker materials)
Waterjet cutting (can cut without creating heat-affected zones)
Mechanical cutting (shearing, sawing, and punching)
Welding joins metal pieces together by applying heat, pressure, or both. Common welding processes include:
MIG (Metal Inert Gas) welding
TIG (Tungsten Inert Gas) welding
Stick welding
Spot welding
Electron beam welding
Machining removes material to create precise shapes and features. Key machining operations include:
Turning (creating cylindrical parts)
Milling (cutting complex shapes and surfaces)
Drilling (creating holes)
Grinding (achieving fine finishes and tight tolerances)
Sheet Metal Fabrication Techniques
Metalworking, also called sheet metal fabrication, deals primarily with various thin sheets of metals, usually ranging from 6 to 25 hundredths of a millimeter in thickness. The following techniques are used to accomplish the sought-after results:
Bending – Forming Angles in Sheet Metal By applying. Pressure with Brakes
Forming - The Process of Shaping Sheet Metal into Three-Dimensional Forms
Drawing – The Process of Pulling Sheet Metal into Die Cavities to Form Particular Shapes
Stamping - Ductile Cutting of Sheet Metals Using Powerful Die Presses. This is Done in One Operation.
Punching – Producing Holes or Cut Outs in the Metal Sheets.
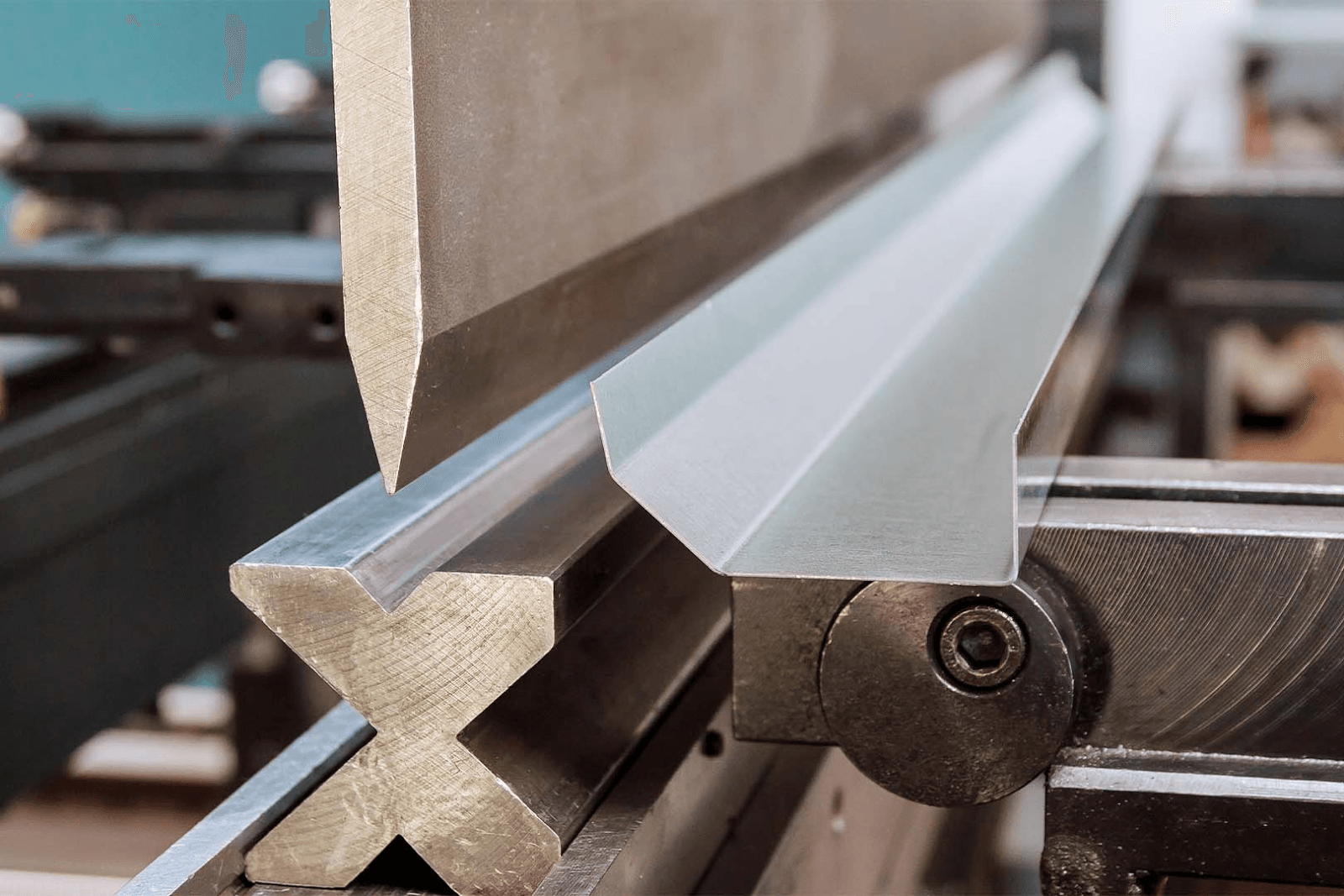
Although it is used by many industries, sheet metal fabrication is used predominantly in aviation, automotive, and electronics due to their need for lightweight and strength.
Advancements in Metal Fabrication Technologies
Due to new technological innovations, metal fabrication is one of the fastest-paced evolving industries. Examples of innovations include:
Additive Manufacturing: The introduction of 3D printing with metals allows for more complicated designs than traditional methods.
Robotic Automation: Makes Strides in Quality Control, Repeatability, and Speed of Production.
Digital Twins: The ability to make virtual images of the physical processes of how things are fabricated helps optimize them.
AI and Machine Learning: Real-Time Prediction of Maintenance process and streamlining the controlling variables of production.
IoT Integration: Allows monitoring and analyzing the fabrication machinery by connecting the devices across the internet.
Today, technology is changing the perception of metal work from a physical, labor-intensive task to an innovation-filled, advanced industry that blends talent and tools.
Types of Metal Fabrication
Custom Metal Fabrication Services
Rather than mass producing identical components, custom metal fabrication services focus on providing solutions for the specific requirements of the clients. Such services usually incorporate:
Design assistance: Aid clients in perfecting designs to enhance manufacturability.
Prototyping: Developing test pieces before commencing large scale production.
Small-batch production: Manufacturing specialized components in limited quantities.
Complex assemblies: Fabricating multi-part systems with varying techniques and methods for intricate parts.
Specialty materials handling: Dealing with exotic or difficult-to-process metals and materials.
Custom metal fabrication is one of the most rapidly growing sectors within the metal fabrication industry. As per research data, since 2020 this sector has seen an annual growth of approximately 3.5% indicating an increasing demand for various components across many industries.
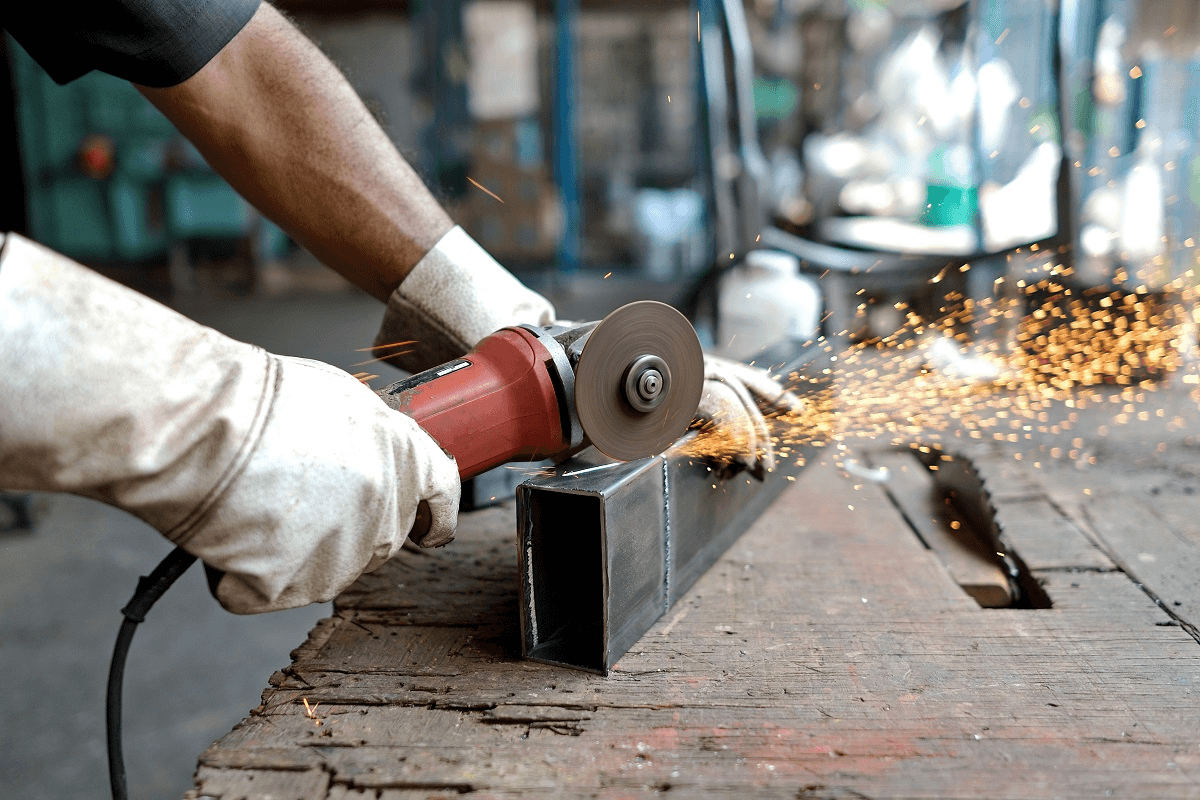
Differences Between Industrial And Commercial Fabrication
Metal fabrication applies to both the industrial and commercial sectors with basic differences such as:
1. Industrial Fabrication:
Deals with heavy machinery, parts, and other infrastructure
Focuses on survivability and strength
Usually requires thicker and bigger materials and parts
Functionality is key compared to aesthetics
Examples include pressure vessels, industrial framed equipment, and structural supports.
2. Commercial Fabrication:
Deals with consumer and business products
Equally stresses useful features and looks
Frequently uses finishing techniques to enhance looks
Thinner, more delicate, and intricate designs are also sometimes employed
Retail display units and other architectural furniture are examples.
3. Common Metal Fabrication Materials
Metal fabricators use various types of materials with different properties and applications, including:
Steel is the most fabricated metal because it is affordable and strong.
Stainless Steel: This corrosion-resistant alloy is primarily used outdoors, in food processing, and medical facilities.
Aluminum: This light material is famous in the automotive, aerospace, and even consumer goods.
Copper: Known to be a great conductor of electricity and heat, copper is mostly used in electronics and HVAC systems.
Brass: This is a corrosion-resistant alloy with good sound properties.
Titanium: Known for its strength and lightweight nature, it is used in aerospace and military medical devices.
Exotic alloys like Inconel, Hastelloy, and titanium are designed for extreme environments.
Selecting the material is based on the environmental exposure, cost constraints, weight considerations, strength requirements and other factors.
Application and Case Studies
A Deep Dive Into The Practical Uses Across Numerous Industries
Almost all industries have requirements for metal fabrication, including:
Construction:
Custom architectural pieces
Complete assemblies of HVAC units
Railing and staircase systems
Frameworks of structural steel
Automotive:
Exhaust system components
Body-chassis of vehicles
Unique pieces and test samples
Aerospace:
Parts of aircraft structures
For engine parts
Various fittings in the internal sections of the airplane
Energy:
Components for mounting solar panels and wind turbines
Equipment used for oil and gas extraction
Agriculture:
Components of farm equipment
Storage appliances like silos
Consumer Goods:
Appliance housings
Furniture frames
Electronics enclosures
Case Studies of Successful Metal Fabrication Projects
Case Study 1: Sustainable Building Integration
A custom fabricator partnered with an architectural firm to create a unique facade system for a LEED-certified office building. The project required precision-cut aluminum panels with integrated solar collection capabilities, demonstrating how metal fabrication contributes to sustainable building practices.
Case Study 2: Rapid Response Manufacturing
During supply chain disruptions in 2023, a medical equipment manufacturer worked with a local fabricator to produce critical stainless steel components for ventilators. The fabricator's ability to quickly retool and produce complex parts highlighted the flexibility of custom fabrication services during crisis situations.
Choosing a Metal Fabrication Service
Factors to Consider When Selecting a Fabricator
When selecting a metal fabrication partner, consider these key factors:
Capabilities and Equipment: Ensure the fabricator has the necessary machinery and expertise for your specific project
Quality Certifications: Look for ISO certifications and industry-specific qualifications
Material Experience: Verify experience working with your required materials
Design Support: Assess their ability to assist with design optimization
Production Capacity: Confirm they can handle your volume requirements
Lead Times: Understand their typical turnaround times
Cost Structure: Compare pricing models and request detailed quotes
Communication: Evaluate responsiveness and communication clarity
Importance of Customization and Expertise
The value of specialized expertise in metal fabrication cannot be overstated. Projects with unique requirements benefit from fabricators who understand not just the technical aspects of metalworking but also the specific needs of your industry.
"The difference between a good fabricator and a great one often comes down to their willingness to truly understand your application," notes James Chen, Production Manager at Precision Metal Solutions. "A fabricator who asks detailed questions about how the component will be used can prevent costly issues down the line."
Custom fabrication services can optimize designs for:
Material efficiency (reducing waste and cost)
Manufacturing simplicity (lowering production time)
Structural integrity (ensuring performance)
Assembly integration (simplifying installation)
Maintenance accessibility (improving long-term serviceability)
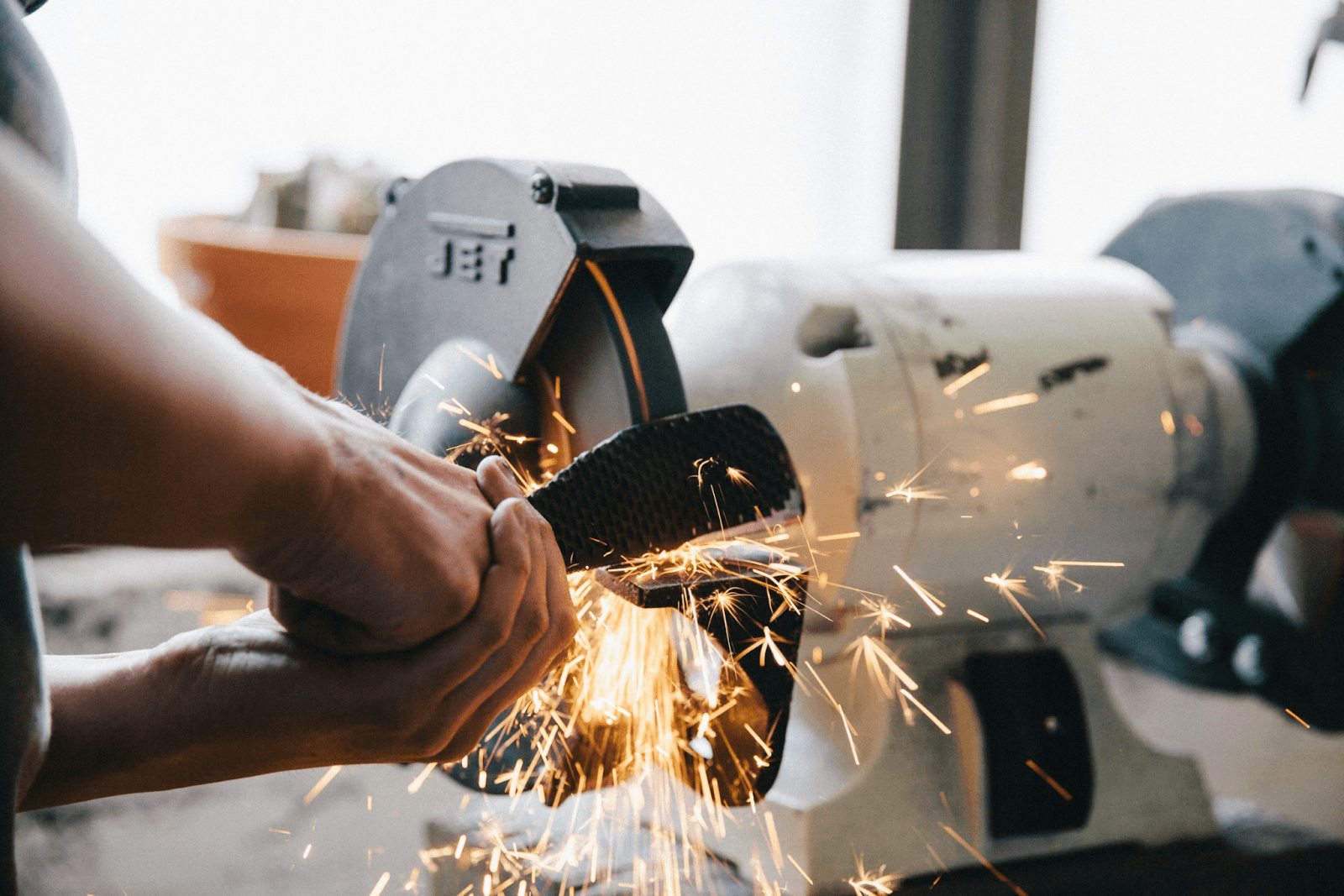
Conclusion
Metal fabrication represents a vital link in the modern manufacturing and construction ecosystem. From simple brackets to complex aerospace components, fabricated metal products form the backbone of countless industries. Understanding the processes, materials, and capabilities involved in metal fabrication can help you make more informed decisions when sourcing components or planning projects.
As we move further into 2025, the metal fabrication industry continues to evolve with new technologies and techniques while maintaining the core craftsmanship that has defined it for generations. Whether you're looking for custom solutions or standard components, knowing what to look for in a fabrication partner can make the difference between a successful project and costly setbacks.
For those in the construction industry or related fields, developing relationships with skilled metal fabricators can provide a competitive advantage through access to custom solutions, technical expertise, and responsive manufacturing capabilities.
FAQ's
What is the meaning of metal fabrication?
Metal fabrication is the process of creating metal structures or products by cutting, bending, and assembling raw metal. It involves transforming metal sheets, bars, or profiles into finished items through various techniques including welding, machining, forming, and finishing.
What does a metal fabricator do?
A metal fabricator takes raw metal and transforms them into finished products as per specifications. Their work includes reading and interpreting blueprints, cutting and shaping metals using various tools and machines, welding components together, and applying finishes. They may work on projects ranging from simple brackets to complex structural components.
What are the three types of metal fabrication?
The three main types of metal fabrication are:
Structural fabrication - Creating frameworks and support structures for buildings and infrastructure
Commercial fabrication - Producing components for consumer products and commercial applications
Industrial fabrication - Manufacturing parts for heavy machinery, equipment, and industrial systems
What is an example of metal fabrication?
A common example of metal fabrication is the production of HVAC ductwork. Sheet metal is cut to specific dimensions, then bent and formed into rectangular or cylindrical ducts. Seams are joined through welding or mechanical fastening, and flanges are added for connection points. The completed ductwork is then installed in buildings to distribute heated or cooled air.
Is metal fabrication the same as welding?
No, metal fabrication is not the same as welding, though welding is an important process within fabrication. Metal fabrication encompasses the entire process of creating metal products, including cutting, forming, machining, and assembly. Welding is specifically the technique of joining metal pieces together through the application of heat or pressure. In other words, welding is one of several techniques used in the broader discipline of metal fabrication.