The industrial sector continues to dynamically evolve. While, at the same time, it has an enormous impact on the construction, manufacturing, and fabrication industries when hiring skilled welders. Due to the increase in infrastructure projects and manufacturing needs, there is a higher demand for welders, but professionals are in short supply. That makes us the one-stop solution provider. In this blog we address solutions to hire welders, discuss staffing problems, and provide opportunities for flexible recruitment services to temporarily staff based on the requirements of your business.
Needs for the Welding Industry's Current Trends
The welding industry continues to experience substantial growth. According to the American Welding Society, there’s plenty of demand, and an insufficient workforce. Anticipated demand for welding services has increased due to growth of infrastructure projects. This further exacerbates the current workforce projection where skilled workers in their middle age will retire and younger entrants are in short supply.
“As aging welders move into retirement, there aren't enough younger entrants to fill in this gap. This leads to a shortage due to the ‘silver tsunami,” remarks Industrial Staffing Solutions Recruitment Director Maria Rodriguez.
Multiple reasons have been identified for this growth in demand:
Investment in infrastructure leading to construction activities
The trend of manufacturing relocating services back to North America
Growth in the energy industries requires professional with welding skills
Sophisticated manufacturing processes that demands increased skill levels
Branches of Welding
There is a wide variety of branches within welding, and each differs in terms of the necessary skills and certification requirements:
Entry-Level Positions:
Production Welders: Perform repetitive welding tasks in a factory setting.
Welding Assistants: Help certified welders with larger projects.
Tack Welders: Place temporary welds to hold parts together.
Specialized Roles:
Pipe Welders: We specialize in pipelines and related aspects of the plumbing, oil, and gas industry.
Structural welders: Focus on building-related frameworks and other construction projects.
TIG Welders: Carry out precision welding for aerospace and automotive industries.
Underwater Welders: Perform underwater (diving) welding work.
Advanced Positions:
Certified Welding Inspectors: Examine welds to ensure standards and other compliance are met.
Welding Engineers: Determine how welds should be assembled and formulate procedures.
Robotic Welding Technicians: Maintain and program machinery that feeds automatic welders.
Tips for recruiting welders
Using specialist welding staffing agencies
Using welding staffing agencies like Flexcrew that specialize in openly advertised vacancies is advantageous to employers who socially recruit welders.
Access to ready-to-use verifiable skill databases: Employment agencies assist with databases of employed welders with relevant qualifications and skills.
Reduced Hiring Timeline: Specialized agencies can help cut the average time-to-hire for welders by 40%.
Skill Verification: Reputable agencies perform practical evaluations to validate welding skills before placement.
Compliance Management: Tips verify relevant certifications, legal work status, and training certifications in safety.
Case Study: Using a welding staffing agency, Western Fabrication reduced its hiring time from 45 days to 12 days. This enabled them to meet critical project deadlines.
Temporary Welder Recruitment Services
Temporary staffing solutions, such as those offered by FlexCrew, provide the flexibility businesses need to adapt to changing project demands.
Project-based staffing: Increase or decrease the size of your workforce depending on specific projects.
Try-before-you-hire: Test welders’ skills and cultural fit into the business before issuing permanent contracts.
Seasonal capacity management: Meet organizational needs during peak production cycles without long-term engagements.
When choosing recruiters offering these services, look for:
Their specialization is in industrial and construction trades.
Spatial coverage relevant to areas where your projects are based.
Verification for relevant skills and certifications.
Compliance with safety training and corrective measures.
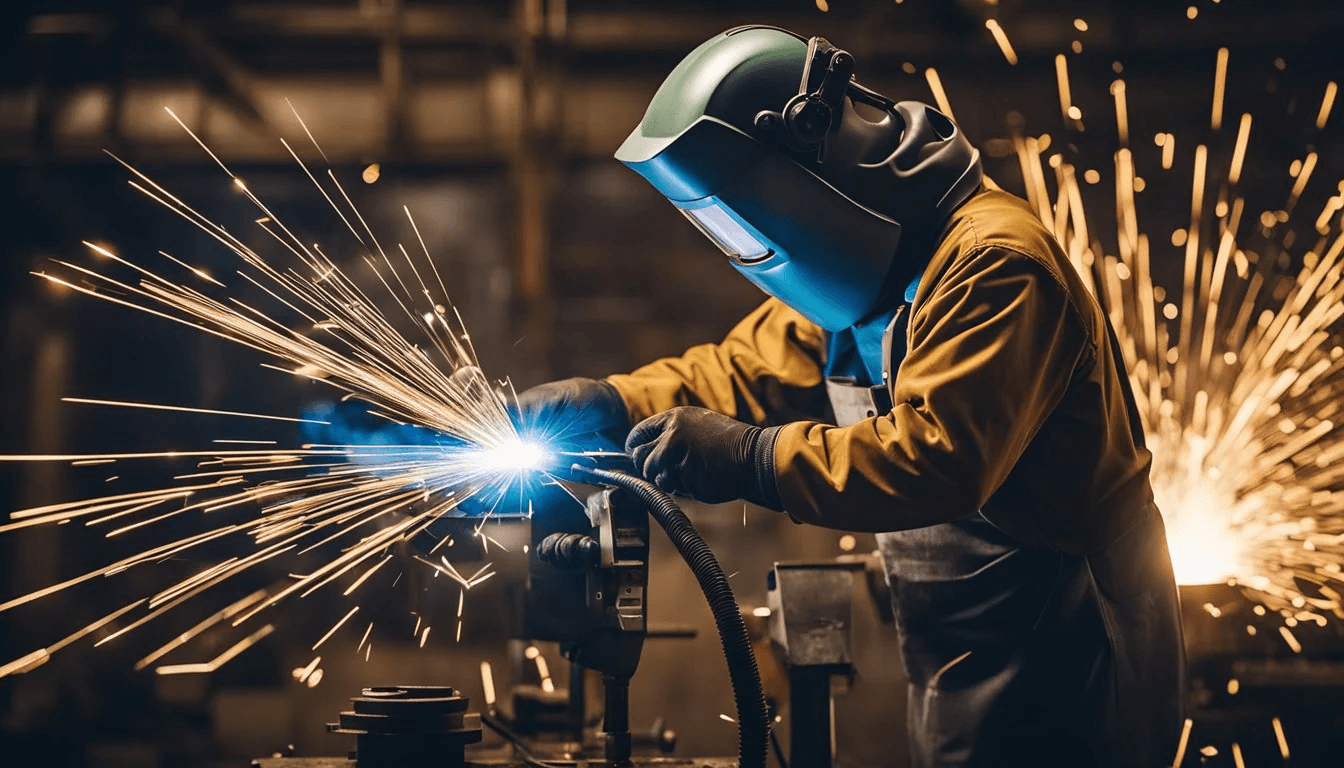
Most Effective Strategies for Recruiting Skillful Welders
Creating Appropriate Job Advertisements
Writing a job description that matches the requirements is vital as it helps you find qualified applicants:
Key Features:
Duties and Responsibilities of the Welder, including experience with required welding techniques (MIG, TIG, Stick, Flux Core,) Material Types Worked with, Such as (steel, aluminum, stainless.
Necessary Qualifications, including certifications such as (AWS, ASME, API)
Detailed work environment (Field vs. Shop, Indoors vs. Outdoors)
Relevant Pre-employment Safety Training and Procedures
Pro Tip: Include information about your equipment and technology to attract welders interested in working with advanced systems.
Offering Competitive Compensation
Compensation remains the primary factor influencing welders' employment decisions:
According to the Bureau of Labor Statistics, the median annual wage for welders was $47,010 in 2024, with the top 10% earning more than $71,000. However, specialized welders in high-demand sectors can command significantly higher salaries:
Pipeline welders: $75,000-$90,000
Underwater welders: $100,000-$200,000
Traveling industrial welders: $75,000-$150,000
Beyond base pay, consider offering:
Performance bonuses for quality and productivity
Per diem for travel assignments
Comprehensive benefits, including health insurance and retirement plans
Tool allowances and safety equipment provisions
Promoting Career Development Opportunities
Today's welders seek more than just a paycheck—they look for opportunities with career advancement:
"Companies that invest in their welders' continued education and certification advancement see 35% higher retention rates than those that don't," notes James Wilson, Director of the American Welding Institute.
Effective development programs include:
Certification support for advanced welding processes
Cross-training opportunities across different welding techniques
Mentorship programs pairing experienced welders with newer talent
Clear pathways to leadership roles, like foreman or supervisor
Technology training for new equipment and processes
Overcoming Common Hiring Challenges
Addressing Skill Gaps
The welding skills gap require proactive approaches:
Apprenticeship programs: Develop structured training combining classroom instruction with hands-on experience.
Partnerships with technical schools: Create pipelines for emerging talent through curriculum input and internship opportunities.
In-house training academies: Some larger companies have established their welding schools to train employees to their specific standards.
Competency-based hiring: Focus on core skills and aptitude rather than years of experience alone.
Navigating High-Demand Locations
Some regions may present higher hiring challenges due to concentrated industrial activity:
California's construction boom has created intense competition for welders, with companies offering signing bonuses up to $5,000.
The Gulf Coast energy sector demands specialized welders for petrochemical applications.
Midwest manufacturing hubs compete for skilled fabrication welders.
Regional strategies include:
Relocation assistance packages
Housing allowances for temporary assignments
Higher compensation reflecting the local cost of living
Flexible scheduling and remote work options were feasible
Conclusion
Successfully hiring welders in 2025 requires a multifaceted approach combining competitive compensation, career development opportunities, and flexible staffing solutions. By understanding the current market dynamics and implementing strategies outlined in this guide, your business can overcome challenges of welder recruitment and build a skilled, reliable workforce.
The most successful companies view welder recruitment as a continuous process rather than a one-time activity. You can create sustainable talent pipelines to support your business growth despite the ongoing skilled labor shortage by establishing relationships with staffing agencies, technical schools, and industry associations.
Key Takeaways
The welding industry faces a significant shortage of qualified professionals
Specialized staffing agencies can reduce hiring time and ensure quality
Competitive compensation must include benefits beyond base salary
Career development opportunities significantly improve retention
Regional strategies may be necessary for high-demand locations
A combination of temporary and permanent staffing provides flexibility
FAQ
How much do welders charge per hour?
Welders typically charge between $25 to $40 per hour for standard work, while specialized welders may command $50-$100+ per hour. Rates vary significantly based on certification level, specialization, geographic location, and project complexity. Union welders generally earn higher hourly rates than their non-union counterparts.
Do welders make 300k a year?
While most welders don't earn that much, certain specialized positions can approach this figure. Underwater welders working in hazardous conditions, pipeline welders on remote projects with extensive overtime, and highly specialized welders in the oil and gas industry can earn $150,000-$250,000+ with per diem, hazard pay, and overtime.
Are welders still in high demand?
Yes, welders remain in extremely high demand across multiple industries. The American Welding Society projects a shortage of 400,000 welders by 2026. This demand is driven by infrastructure projects, manufacturing growth, and an aging workforce, with fewer young people entering the profession to replace retiring welders.
Can a welder make $200,000?
Yes, some welders can earn $200,000, though this represents the upper echelons of the profession. These earnings typically come from specialized roles like underwater welding, remote pipeline work, or nuclear facility welding, often include substantial overtime, hazard pay, and per diem allowances rather than base salary alone.
What are the best places to hire welders?
The most effective channels for hiring welders include:
Specialized industrial staffing agencies
Technical and trade schools with welding programs
Industry-specific job boards like Fabricators & Manufacturers Association
Welding union halls and apprenticeship programs
Social media groups focused on welding professionals
Industry trade shows and career fairs
Employee referral programs leveraging your existing workforce