In today's industrial landscape, welding and fabrication stand as cornerstone processes that quite literally hold our modern world together. From the towering skyscrapers that define city skylines to the vehicles we drive and the infrastructure we rely on daily, these specialized techniques play an essential role in creating the physical framework of our society. But what exactly distinguishes welding from fabrication, and how do these processes work together to shape the materials that build our world?
Understanding Welding and Fabrication
The relationship between welding and fabrication is intimate yet distinct. While often mentioned together, they represent different aspects of metalworking that complement each other in the creation of metal structures and products.
What is Welding?
Welding is a procedure that joins different or similar materials using heat, pressure, or both. It is closely related to manufacturing and is associated separately with metalwork. The base items are first melted using heat; in some cases, additional materials are melted to form a pool of molten metal below. This, along with the cooled extract, makes the joint firm.
In today's world, most welding is done in the following ways:
MIG, metal inert gas welding: Often referred to as Gas Metal Arc Welding (GMAW), this approach employs a continuously fed wire electrode and a protective gas. It is easy to learn, fast, and versatile, making it common in several areas.
TIG, Tungsten Inert Gas Welding: Gas Tungsten Arc Welding (GTAW). Visually, this precise process is appropriate when dealing with fine, thin materials or scenarios needing high-quality welds, as it utilizes a non-consumable tungsten electrode for welding.
Stick welding: Known formally as Shielded Metal Arc Welding (SMAW), this process implements a flux-covered electrode that forms a gas sheath once heated. It is ideal for a construction site; it is portable and works well under open-air conditions.
Flux Cored Arc Welding (FCAW) is like MIG welding but with a tubular wire filled with flux. This type excels relative to other types of welding when dealing with thicker materials and outdoor sites.
The American Welding Society states that approximately 50% of industrial welding applications use MIG welding, owing to its utility and versatility.
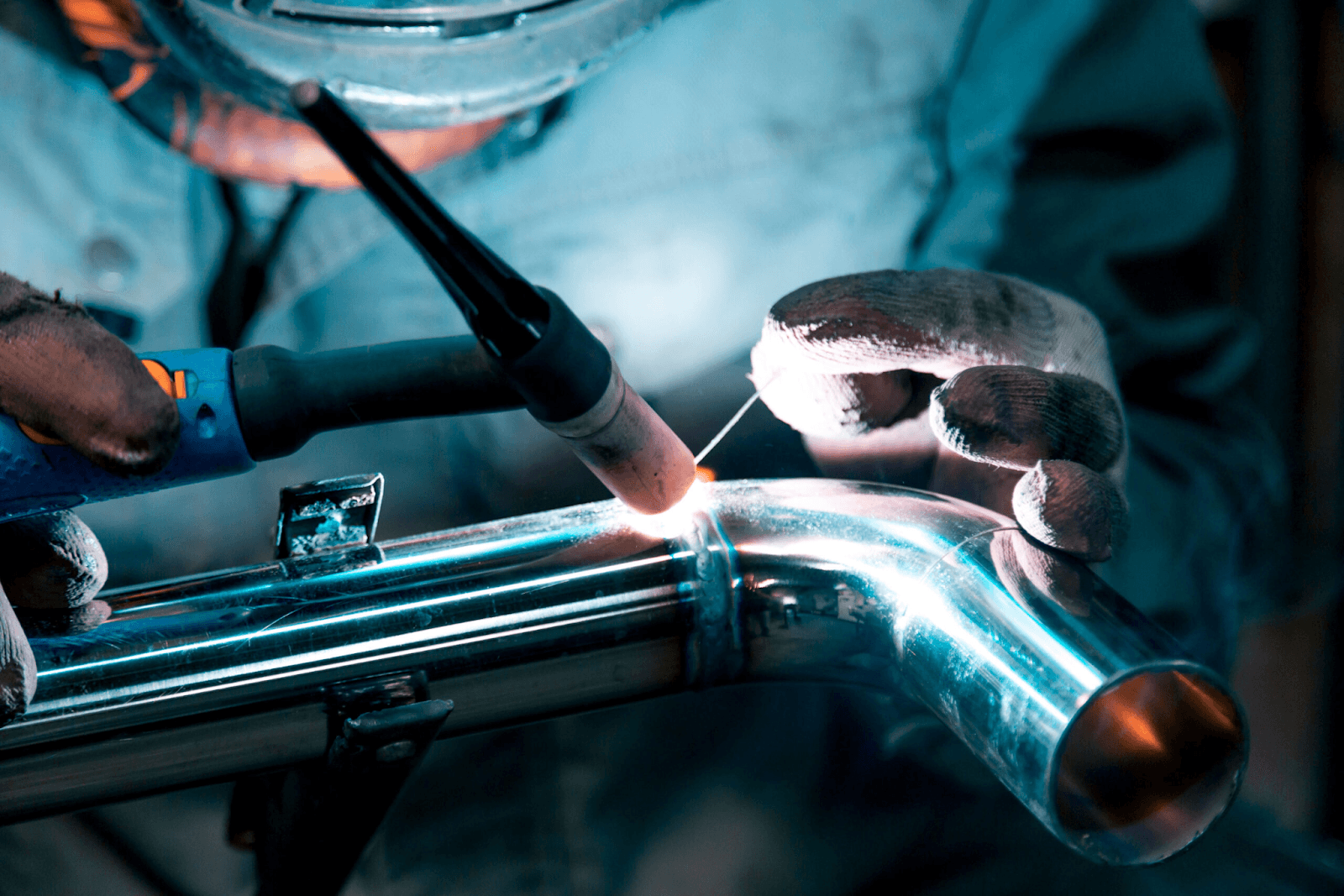
What is Fabrication?
Fabrication is concerned with the greater encompassing principle of the formation of metal goods from materials to be transformed. Welding is integrated in the scope of fabrication, but in fact, there are many other processes involved, including:
Cutting: Shaping metal pieces using lasers, plasma, or water jets.
Bending: Forming metal to specific angles or curves using press brakes.
Assembling: The joining together of the various cut and bent pieces through a variety of means, including welding, riveting, bolting, and adhesive bonding.
Finishing: The final process of grinding, polishing, painting, or powder coating to make a part visually appealing.
The welding process embodies the fabrication of a product that begins from raw materials and culminates in a finished product.
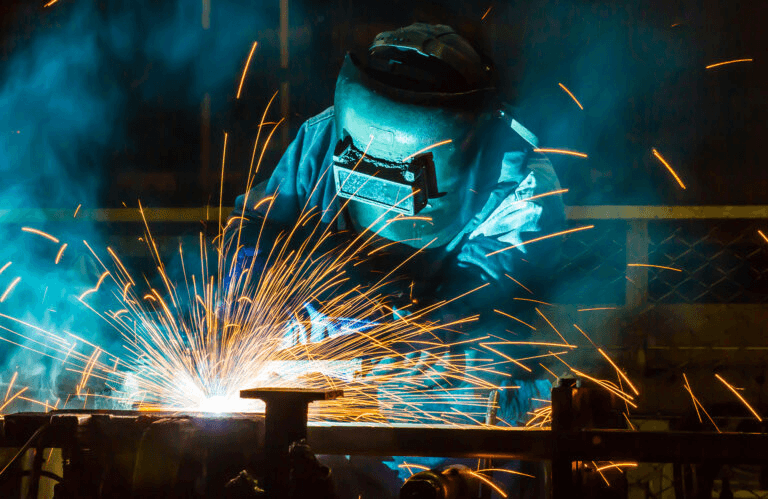
Key Welding and Fabrication Techniques
The methods that are applied in welding and fabrication differ greatly from one project to another. Factors such as material types and industry standards impact the methods used.
Industrial Welding and Fabrication Services
The services offered in industrial settings are tailor-made to suit the exact needs of clients in terms of accuracy, speed and strength. These services usually incorporate:
Structural Welding: The construction of primary structural elements of buildings, bridges, and industrial structures.
Pipe Welding - Connecting pipes in plumbing, oil and gas, or chemical processing industries with strict compliance to code regulations.
Custom Fabrication - Creating parts for industrial machinery and pieces of architecture as per client requirements including custom design work.
Pressure Vessel Fabrication - Building vessels that hold gases or liquids at relative pressures to the environment and require certification along with adhering to rigid safety regulations.
In industrial welding and fabrication, safety and quality control is vital. . The Bureau of Labor Statistics indicates that the enforcement of stringent safety measures has cut injuries in metal fabrication by 22% over the last ten years.
Welding and Fabrication On-Site Services
Unlike off-site worksites, on-site services offer flexibility for projects that cannot be moved, such as large structures or pieces that need to be assembled on-site.
Some of the industries that use onsite welding and fabrication services include:
Construction: For structural steel assembly, reinforcements, and other building repairs during construction.
Mining: Maintenance and repair of heavy equipment that is not easily movable to a shop.
Shipbuilding: Installation of large vessel components that must be welded on-site in shipyards.
Energy: Maintenance and installation of pipelines, power plants, and renewable energy infrastructure systems.
On-site welding faces distinctive challenges like the weather, accessibility, and power supply. Skilled workers with mobile welding units, gas and power generators, and other specialized equipment can meet these challenges and provide exceptional work in all settings.
Career Opportunities within Welding and Fabrication
Is there a demand for welding and fabrication?
Yes, as far as the welding and fabrication industry is concerned, there will be considerable job openings in 2025. From 2020 to 2030, the employment of welders, cutters, solderers, and brazers is expected to grow by 8%, more than the average for many occupations, as per the US Bureau of Labor Statistics.
This positive outlook stems from several sources:
Investment on Infrastructure: Construction of new infrastructure creates steady employment opportunities for skilled welders and fabricators through ongoing government programs.
Resurgence In Advanced Manufacturing: Domestic need for metalworking specialists has risen due to shifting manufacturing exports to the United States.
Shortage Of Skilled Workers: An aging population indicates loss of experienced manpower, , this with a reduced influx of welders is bound to create a shortage of skilled workers.
Salary trends remain competitive, with the median annual wage for welders and fabricators at approximately $47,000 as of 2025, with specialized welders in high-demand sectors like underwater welding or pipeline work earning well over $100,000 annually.
Skills and Education Needed
Accomplishing welding and fabrication tasks require a mix of hands-on skills, technical education, and criticism:
Core skills:
Dexterity and precise hand-eye coordination
Spatial intelligence, along with the ability to understand blueprints
Detailed tasks and precise work
Sustained physical demand and strength
Strategic issue resolution
Basic calculations
Maintaining safety standards
Education Options:
Technical/Vocational Schools: Structure programs of 6 months up to 2 years, emphasizing advanced training.
Community Colleges: Offering associate degrees that provide practical skills with theoretical elements.
Apprenticeships: Sponsorship from unions or employers for practical training under skilled professionals.
Military Training: Welding training is available in all military branches and it relates well to civilian employment.
Valuable Certifications:
American Welding Society (AWS) certifications
American Society of Mechanical Engineers (ASME) certifications
Certified Welding Inspector (CWI) credential
Specialized certifications for particular welding processes or materials
Emerging Technologies in Welding and Fabrication
Innovations abound in the welding and fabrication world, with technologies and several new practices redefining the industry.
Robotic Welding: In large manufacturing facilities, Automated systems now perform around 50 percent to 90 percent of all welding tasks, offering unmatched precision and sterility.
Artificial Intelligence: AI-powered systems that monitor quality standards can observe welding imperfections in real time, increasing the workflow efficiency and quality of the final product.
Augmented Reality (AR): AR welding helmets assist trainees by providing real-time feedback regarding their technique and head placement, thus streamlining procedure training and accuracy.
Additive Manufacturing: Certain fabrication processes are literally being 3D printed with metal, changing the scope of what's possible with traditional methods.
Advanced Materials: The development of new alloys composite materials permits to be welded by new techniques which drives innovation in equipment and methodology.
These technologies are not replacing human welders but rather enhancing their capabilities and changing the skill sets required for success in the field.
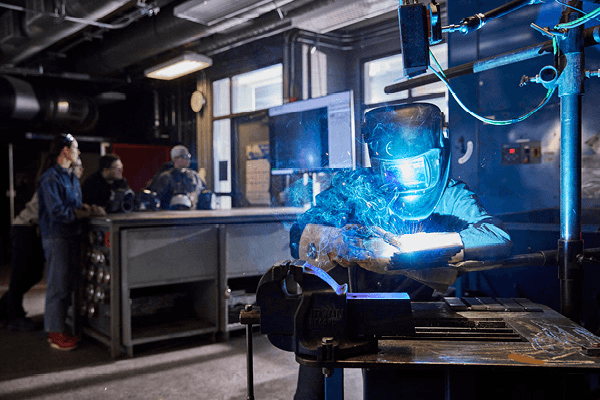
Sustainable Practices
Environmental consciousness has made significant inroads in welding and fabrication, with sustainable practices becoming increasingly prevalent:
Energy-Efficient Equipment: Modern welding machines consume up to 40% less energy than models from a decade ago.
Waste Reduction: Computer-aided design and nesting software optimize material usage, reducing scrap by up to 30%.
Recycled Materials: Many fabricators now prioritize recycled metals, reducing the environmental impact of raw material extraction.
Low-Emission Processes: Advances in welding technology have reduced harmful emissions, improving both environmental impact and worker safety.
Companies like Lincoln Electric and Miller have taken leadership positions in sustainable welding, developing equipment that minimizes environmental impact while maintaining or improving performance characteristics.
Conclusion
Welding and fabrication remain indispensable processes in our industrial society, combining traditional craftsmanship with cutting-edge technology. As we move through 2025, the field continues to evolve, offering robust career opportunities for those willing to develop the necessary skills and adapt to changing technologies.
The distinction between welding (joining materials through fusion) and fabrication (the complete process of creating metal products) highlights the complementary nature of these disciplines. Together, they form the backbone of manufacturing, construction, and countless other industries that build our physical world.
For those considering a career in this field or industries looking to leverage these essential services, understanding the fundamentals, techniques, and future directions of welding and fabrication provides a solid foundation for informed decision-making and continued growth.
FAQ
What is welding and fabrication?
Welding is a process that joins materials, typically metals, by causing fusion through heat, pressure, or both. Fabrication is the broader process of creating metal products from raw materials, which includes cutting, bending, assembling (often through welding), and finishing.
Is welding and fabrication a good career?
Yes, welding and fabrication offer promising career prospects with above-average growth projections, competitive salaries, and job security. The industry faces a skills gap as experienced workers retire, creating opportunities for new entrants with proper training and certifications.
What does a welder and fabricator do?
Welders join metals using various welding processes, while fabricators handle the entire process of creating metal products—from cutting and shaping raw materials to assembly and finishing. Many professionals perform both roles, particularly in smaller operations.
What are the four types of welding?
The four most common types of welding are:
1) MIG (Metal Inert Gas) welding, which uses a continuously fed wire electrode
2) TIG (Tungsten Inert Gas) welding, which uses a non-consumable tungsten electrode
3) Stick welding, which uses a flux-covered electrode
4) Flux-Cored Arc Welding, which uses a hollow wire filled with flux.
What industries benefit from welding and fabrication?
Numerous industries rely on welding and fabrication, including construction, manufacturing, automotive, aerospace, shipbuilding, energy (oil, gas, and renewable), mining, agriculture, and infrastructure development. Essentially, any industry that works with metal components benefits from these processes.