Brick by brick, stone by stone - masonry contractors create the structures we admire every day. These skilled professionals combine artistic vision with technical expertise to build features that don't just look beautiful but stand the test of time.
The masonry world in 2025 is buzzing with activity. Traditional techniques now work alongside innovative approaches, giving homeowners, building developers, and aspiring contractors more options than ever. From classic brick facades to custom stonework, masonry adds character and value to any property.
This comprehensive guide explores everything you need to know about masonry contractors today—from their diverse service offerings and pricing factors to licensing requirements and emerging industry innovations.
Services Offered by Masonry Contractors
Professional masonry contractors provide much more than just brick-laying: they cater to many residential and commercial clients with their specialized services.
New Construction Services
Masonry contractors excel in creating new structures using various materials:
Brick masonry: This might be the oldest form of construction, yet it remains relevant: walls, facades, and even whole clay or concrete stone buildings can be constructed using brick regions. Modern methods of brick masonry construction include innovative approaches to enhancing the thermal and waterproofing properties of the structures.
Stone masonry: A more refined service utilizing natural stones, such as limestone, granite, and marble, or artificial stone veneer, to make notable design features. Stone masonry is often charged at a premium due to the high cost of materials and the specialized skilled labor at hand.
Concrete block masonry: Commonly used in commercial structures and foundations, concrete blocks are extremely durable, and their price is more economical than that of other stone materials.
Glass block installation: These blocks can be used to construct walls that are both beautiful and allow light to pass through while keeping the room private. Specialized masonry contractors install these blocks.
The following are examples of typical new construction projects:
Load-bearing and Non-load-bearing walls
Building Facades and Exteriors
Retaining Commercial Building Structures and
Decorative Garden Walls.
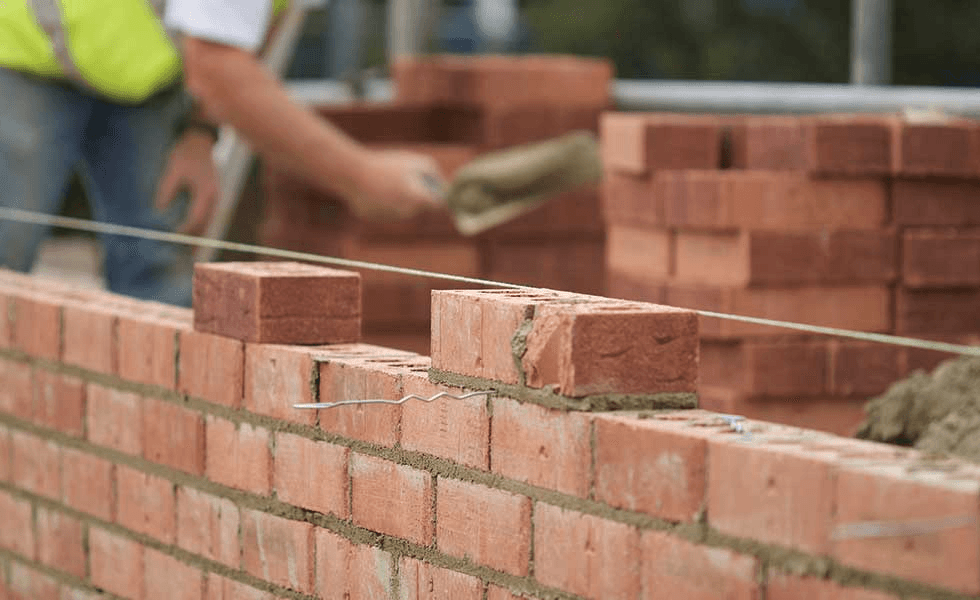
Restoration and Repair Services
Masonry includes the preservation and restoration works related to construction:
Tuckpointing: This preserved form of mortar joint repointing technique includes partial removal of old and decayed mortar joints and replacing it with fresh mortar material. Apart from making joints look good, tuckpointing enhances water drainage and structural damage prevention.
Chemical cleaning: Professional masonry contractors carry appropriate cleaning chemicals that permit the elimination of stains, efflorescence, and biological growth without damaging the masonry surface.
Restoration and Rebuilding: For contractors to come up with and/or restore heavily damaged structures, they must dismantle and set up portions of them while respecting the construction's historical center and the framework’s soundness.
Crack Repair: Cracks, when filled in masonry, aid in preventing water from getting through and further disintegrating the structure. Repair methods can range from simple and elegant mortar crack props to complex and methodical structural props.
Waterproofing: Water sealant polymers are applied for dampness proofing and eliminating water impact while servicing as a defense barrier for masonry elements.
Solving these issues is associated not only with aesthetic concepts. Preserving the architectural condition of the building and the infrastructural system of construction damages costly finances.
Custom Projects of Masonry Contractors
Aside from general construction and repair, masonry contractors sometimes focus on particular work areas.
Chimneys and Fireplaces: New and existing fireplaces and chimneys need to be constructed or repaired with a certain level of expertise concerning the principles of the draft, the relevant fire codes, and structural issues.
Patios and Walkways: Construction of elegant outdoor living spaces utilizing concrete, stone, or brick pavers.
Retaining Walls: These are buildings made to hold back eroded soil and make terraced areas that can be used on land with a slope.
Outdoor Kitchens: These have a custom design with stone countertops, ovens, and grills built into the construction.
Decorative Features: These include columns and archways crafted from ornamental stone and add greater magnificence and flair to the architecture.
Such projects often present difficulties that need creative problem-solving and technical skills. For example, implementing outdoor projects in cold climates requires special strategies to manage freeze-thaw cycles, whereas understanding ventilation requirements is crucial for chimney construction.
Cost Factors for Masonry Services
Understanding the cost structure of masonry work helps clients budget appropriately and contractors price their services competitively.
Hourly Rates and Project Fees
Masonry contractors typically charge using one of these models:
Hourly rates: Generally ranging from $35 to $100 per hour depending on location, experience level, and project complexity. Specialized masons with rare skills may command higher rates.
Minimum fees: Most contractors establish minimum project fees between $200 and $1,500 to ensure small jobs remain profitable after accounting for travel, setup, and administrative costs.
Per-square-foot pricing: Common for larger projects like brick walls ($15-30 per square foot) or stone veneer installation ($25-50 per square foot).
Project-based quotes: Comprehensive estimates based on materials, labor, equipment, and project duration.
According to recent industry data, the national average for a standard brick wall installation runs approximately $4,000-$8,000, while stone masonry projects typically start at $10,000 and can exceed $50,000 for extensive work.
Material and Project Complexity
Material selection significantly impacts overall project costs:
Material Type | Average Cost Range (2025) |
Brick siding | $10,000-$22,000 for average home |
Stone veneer | $24,000-$43,000 for average home |
Concrete block | $8,000-$16,000 for average foundation |
Marble | $40-$200 per square foot installed |
Project complexity factors that influence pricing include:
Intricate patterns or designs requiring precise cutting and fitting
Structural reinforcement needs
Height and accessibility challenges
Custom color matching for restoration work
Time constraints requiring accelerated schedules
For example, a simple brick patio might cost $15-25 per square foot, while an elaborately patterned design with multiple colors and custom borders could easily double that price.
Site Preparation and Additional Features
Before commencing with the brickwork, the following preparatory tasks must be completed.
Clearing and excavation consist of vegetation or existing object removal, rock removal, site leveling, or the use of bulldozers.
Grading is leveling the site to prevent water collection.
Foundation work is the incorporation of concrete concentration setting to provide the structure with strength.
Drainage installation includes weeping holes, French drains, and other water control methods.
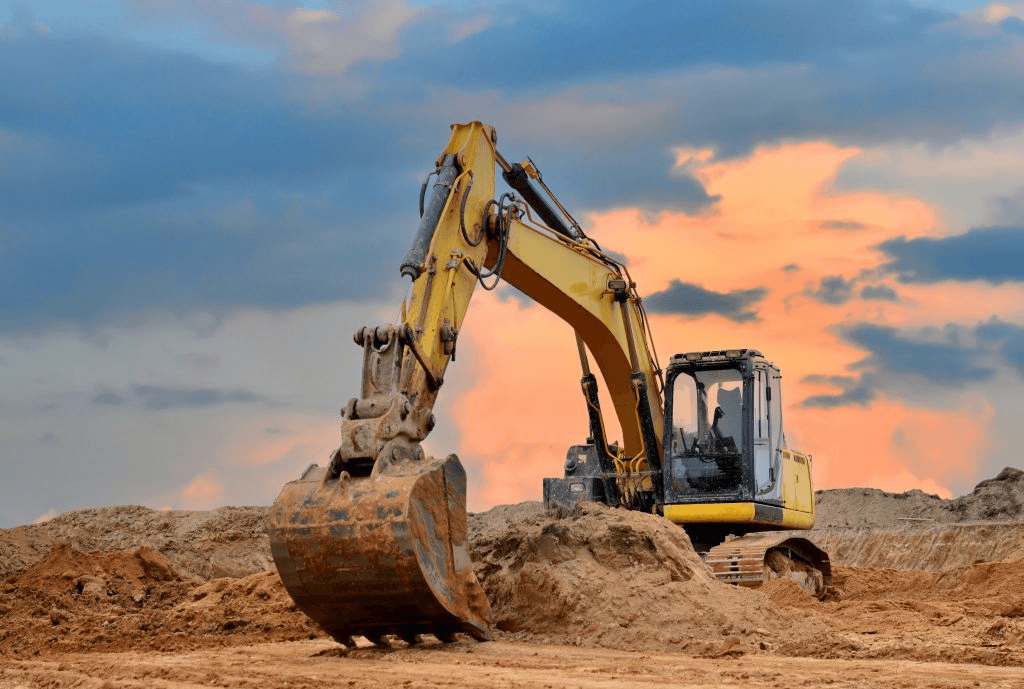
These task costs represent 10% to 30% of the cost of the leading project. However, they must be done to ensure the structure's longevity.
Extra features that increase the price of the project include:
Lights are built into the structure.
Built-in sittings and planters.
Fire features such as BBQ or Fire pits.
Other intricate or fancy treatments or coatings.
Decoration covers, columns, or surfaces.
Customers need to ensure the cost will cover this basic block addition purchasing concerning the plan alternative so, reasonably; an increase does not occur halfway through the project.
Legal Documentation and Licences for Masonry Contractors
Fully fledged masonry contractors are required to meet a myriad of legal requirements that are clearly defined and vary from area to area.
The Stone Mason Licensing Policies within Each State
The rules surrounding masonry contracting differ considerably from one state to the other:
In Florida, there is a two-tiered approach:
Certified contractors are allowed to operate throughout the state.
Registered contractors have to operate within certain local jurisdictions.
Working without a license can lead to fines that exceed $10,000 and possible felony charges.
In Minnesota, residential contractors with earnings above 15,000 must register with the state.
California requires a C-29 specialty contractor license exclusively for licensed masons.
There are local regulations in some municipalities in Texas. However, there are no general licensure legal requirements for contractors in the state.
There are local rules for other states that are equally as permissive. Other freemasonry states require a minimum of 2-4 years of working experience along with the passing of competence exams. There is also an insurance requirement alongside the billing requirement of $150-$500 yearly.
As Michael Johnson, the Executive Director of the Mason Contractors Association of America, said, it’s more than compliance; it’s a liability shield for the business and the customers.
Business Registration and Insurance
For mason contracts, aside from the trade-specific licensing, other requirements need to be satisfied, including:
Filing a business entity (Especially LLC or corporation) with the state's office
Securing an IRS-issued Employer Identification Number
Guarding against risk by obtaining appropriate insurance
- General liability insurance cap ($500,000 – $ 2 million insurance cover)
- Workers’ compensation insurance (required in most states)
- Company vehicle auto insurance
- Additional umbrella policies to safeguard
Avoiding bonding issues:
Performance bonds promise to finish the project.
Payment bonds guarantee subcontractors and suppliers are paid.
License bonds where certain jurisdictions may issue
Keeping proper records and documentation helps in compliance with laws or lures any potential penalties. This gives a competitive edge when tendering for more projects particularly government contracts or commercial works where it is a requirement to give proof documentation.
Safety and Training in Masonry
The kind of work done in masonry is characteristically manual labor, which poses lots of risk and safety challenges that can be managed with sufficient training and rules.
Common Hazards and Safety Protocols
Workers in the field face various physical hazards, including: Still, they are not limited to:
Exposure to Silica dust: Cutting or grinding masonry materials can create airborne respirable crystalline silica, which leads to silicosis and dangers to the respiratory system. Silica standard OSHA has mandates in place where they expect wet cutting or vacuum systems along with the right kind of respirators to be provided.
Fall Hazard: Scaffolding or working from any elevated surface comes with significant risks that could result in a fall. Following OSHA policies, proper fall protection systems are required for any elevated work 6 feet or more from the ground or floor.
Musculoskeletal injuries: Heavy lifting can lead to musculoskeletal injuries like back and joint problems. Assisting the lifting with a tool and using proper lifting methods are crucial preventative actions.
Struck-by hazards: Tools, materials, or equipment can cause serious injuries if they fall or are improperly handled.
Here are some of the fundamental safety measures:
A safety plan for the job site
Maintenance of calendars for periodic safety training and meetings
Wearing personal protective equipment such as:
Head protection
Safety boots
Respiratory shields
Eye protection
Hearing protection
Gloves
Footwear
Inspection of scaffolds
Program for the prevention of heat stress in summer
Cold climate work methods
Industry Certifications and Training Programs
Opportunities for professional growth and advancement for masonry contractors consist of:
The Mason Contractors Association of America offers Certified Masonry Contractors (CMC).
The International Masonry Institute offers Masonry Certification.
Construction Safety OSHA 10-Hour and 30-Hour courses.
Apprenticeship programs typically take 3 to 4 years, including classroom sessions and practical training.
Other specialized training includes:
Techniques for preserving historic masonry
Advanced stone carving and fabrication.
Structural reinforcement techniques
Masonry contractor project management.
Eco-friendly masonry.
“As materials and methods change, there is a great deal of competitive advantage for contractors who spend money on ongoing training,” said International Masonry Institute instructor Lisa Thompson. “An industry does not stand still or slow down; continuous education is a must in this industry.”
Industry Trends and Innovations
The change in architectural style, environmental concerns, and modernization technology have impacted the masonry industry's evolution.
Eco-Friendly Materials and Techniques
Since masonry has become a leading force in sustainability:
Reclaimed and recyclable materials: Salvaged brick and stone are not only eye-catching but also minimize the impact on the environment. The masonry industry that deals with reclaimed materials has been growing by 2020 almost 15% a year.
Low-carbon concrete alternatives: Geopolymer cement and carbon sequestering concrete formulation lower the carbon emissions associated with Portland cement.
Permeable paving systems: Such systems are gaining traction for use in garages, patios, and other places as they permit water infiltration and enable the minimization of runoff, as well as the backing of groundwater recharge.
Living walls: The vertical gardens that aid in enhancing air cleansing and the insulation of the building’s walls are supported by masonry structures.
Thermal mass optimization: Using masonry materials in buildings to capture and utilize heat, then gradually releasing it for energy consumption optimization.
As per the new industry research, there has been an increase of 30% in client requests for projects featuring sustainable masonry practices, especially from eco-friendly commercial customers and extravagant-class housing clients, which has been noteworthy since 2023.
Technological Advancements in Masonry
Masonry and construction are evolving with new technologies for traditional practiced methods:
Prefabricated masonry systems: These are modular wall panels produced in factories, which cut down both labor required on-site and improve installation efficiency by up to 40%.
3D printing applications: New technologies enable advanced geometry with less wastage using a special concrete mixture to custom print specific masonry items.
Advanced modeling software: Programs for designing and Building Information Modeling (BIM) enable better precision during planning masonry construction processes to minimize errors.
Robotic assistance: These are semi-automated systems that help with bricklaying and material handling, which are being developed to counter the shortage of workers while improving quality with greater consistency.
Enhanced material performance: Modernized, and therefore more reliable, engineered masonry units have better thermal insulation, lower weight, and higher durability than their predecessors.
Digital documentation tools: Administrative work is made easier with mobile apps for the management of projects, quality control, and compliance documentation.
Dr. James Williams, Director of the Masonry Innovation Research Center, believes that this "Fusion of digital technology with traditional masonry work layouts our industry’s future”. “These technologies do not eliminate the skilled masons; instead, they support and improve their skills while solving the current workforce problem."
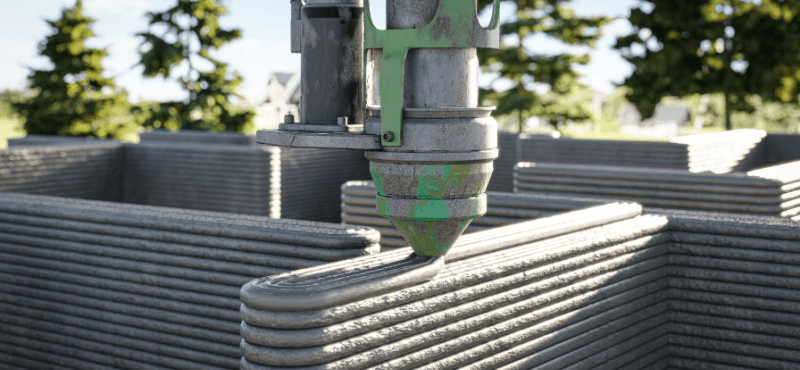
Conclusion
Masonry contractors still form part of the construction industry by combining traditional construction methods and innovative technologies to provide aesthetically appealing and durable structures. To achieve optimal value, clients and other professionals in the industry should appreciate the level of service, the factors that affect pricing, and the legal obligations for professional conduct.
While there is a lack of labor, there is an increase in the use of technology and socially responsible designs that create new opportunities and greater efficiency. Adapting to change is important; therefore, contractors must pay attention to legislation, training, and other pertinent changes to enjoy the benefits.
Whether you're considering a career in masonry, looking to hire a contractor for your project, or seeking to enhance your existing masonry business, the information provided in this guide is a valuable resource for navigating this dynamic and essential trade.
Frequently Asked Questions
How much does a masonry contractor charge per hour?
Masonry contractors typically charge between $35 and $100 per hour, depending on their experience level, geographic location, and project complexity. Specialized masonry work involving intricate designs or historic restoration may command rates at the higher end of this range or beyond. Most contractors also establish minimum project fees ranging from $200 to $1,500 to ensure small jobs remain profitable.
What is a masonry contractor?
A masonry contractor is a specialized construction professional who builds, repairs, and maintains structures using materials like brick, stone, concrete blocks, tile, and mortar. These skilled tradespeople handle projects ranging from decorative features to structural elements, including walls, chimneys, patios, and foundations. Professional masonry contractors typically complete extensive training through apprenticeships or formal education and must maintain appropriate licensing and insurance.
Why is masonry work so expensive?
Masonry work commands premium prices due to several factors: the high level of skill required (typically developed through years of training), the physical demands of the labor, material costs (particularly for natural stone), specialized equipment needs, and the long-lasting nature of quality masonry work. Additionally, proper masonry installation requires extensive site preparation and precise execution to ensure structural integrity and longevity, further contributing to costs. However, the durability and low maintenance requirements of masonry work often make it cost-effective over the lifetime of the structure.
What are the three types of masonry?
The three primary types of masonry are:
Brick masonry: Utilizing fired clay or concrete bricks bonded with mortar, this traditional form offers excellent durability and fire resistance.
Stone masonry: Using natural or manufactured stone, this premium option provides distinctive aesthetics and exceptional longevity.
Concrete masonry: Employing concrete blocks or poured concrete, this versatile approach offers structural strength and cost efficiency.
Each type has numerous subtypes and variations, with selection depending on factors like budget, aesthetic preferences, structural requirements, and local building traditions.
How do I become a licensed masonry contractor?
Becoming a licensed masonry contractor typically requires:
Gaining experience through apprenticeship or employment (usually 2-4 years)
Studying relevant building codes and masonry techniques
Passing state-specific licensing exams covering trade knowledge and business practices
Obtaining proper insurance coverage (general liability and workers' compensation)
Registering your business with state authorities
Securing any required bonds
Requirements vary significantly by state and sometimes by municipality, so contacting your local licensing board is essential for specific guidance. Many successful contractors also pursue additional certifications through industry organizations to demonstrate expertise and gain a competitive advantage.