Construction workforce management’s evolution centers on its greatest asset: people. As the industry navigates skilled labor challenges, evolving safety standards, and technological innovations, effective workforce management has become their cornerstone of success.
Smart construction companies are thriving by implementing digital management tools that streamline operations, creating vibrant safety-first cultures, and developing innovative training programs.
To properly address these issues, this guide dives into the most recommended strategies, tools, and practices of construction workforce management in 2025 and onwards.
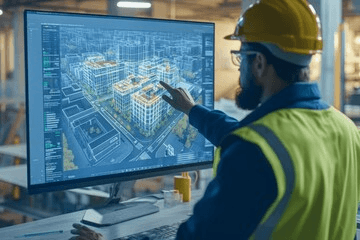
Defining Construction Workforce Management Terms
Scope and Definition
Workforce management includes the processes, procedures, and tools a company employs to use labor best for any construction activity. It includes exams relating to project execution, such as workforce planning, scheduling, skill allocation, timekeeping, performance evaluation, and adherence activities.
Unlike traditional labor management practices, modern construction workforce management adopts a paradigm integrated by technology, conveyors, analytics, and strategic planning – all aimed at delivering higher productivity while safeguarding employee and stakeholder safety and satisfaction.
Maria Rodriguez, Construction HR Director at BuildTech Enterprises, explains, “Construction workforce management isn’t just about scheduling workers anymore – it’s about building a system in which compliance, safety, and budget constraints are respected, and people with adequate skills have access to the right place at the right time.”
Importance and Benefits
Some of the benefits that an organization can get from efficient management of workforce resources are listed below:
Productivity improvement: Well-organized construction teams can enhance productivity by as much as 25%, according to research findings.
Cost savings: Properly managing and allocating workers saves 10-15% dollars in overtime pay.
Greater safety: Well-structured workforce management improves safety by leading to a 30% reduction in workplace accidents.
More timely completion of projects: Projects with good workforce management are completed on time 35% more often than those without.
Favorable employee turnover: Strategic workforce management yields 40% more favorable retention results by such organizations.
Key Challenges in Construction Workforce Management
Labor Shortages and Aging Workforce
According to the Associated Builders and Contractors (ABC), the construction industry needs to hire almost an additional 650,000 employees above the regular level of hiring in 2023. In the meantime, about 41 percent of the existing workforce in construction is estimated to retire by 2031, leaving a large gap in knowledge and experience.
These shortages issues are made worse by:
There is less enthusiasm for pursuing building trades careers among the younger generations
Insufficient training and apprenticeship sponsorships
Other industries competing for skilled workers
Shifts in immigration policy that influence the available workforce
Safety Compliance and Risks
Safety, as always, is a concern because construction work still has the highest fatality rates. According to OSHA:
Construction accounts for 20 percent of all fatalities in the private sector.
Falls remain the number one reason for construction deaths.
More than half of all workers’ compensation claims are made by employees who have worked less than a year.
Achieving strict safety standards and productivity is challenging enough, with new regulations and new workforce members constantly being added.
Project Delays and Cost Overruns
Labor issues constitute the main reason for the delay in time and budget estimates:
91% of construction companies say they experience delays because of insufficient workforce.
Laborers’ remuneration generally represents thirty to fifty percent of the project costs.
Unplanned written overtime sometimes increases labor costs by more than fifty percent.
Rework resulting from skill gaps costs the industry trillions of dollars every year.
Strategies for Effective Workforce Planning
Skill Mapping and Demand Forecasting
Progressive construction companies are already making sophisticated investments in skill mapping techniques to keep track of each employee’s certificates, experiences, and skill level. This cashless system enables project supervisors to:
Assign workers to tasks for which they have appropriate qualifications.
Spotlight skill deficiencies well in advance of deadline projections.
Design skill-training courses for high-priority tasks.
Formulate precise expenditure estimates on workforce services.
Simply counting heads is no longer an effective method of demand estimation. New methods propose:
Analytical examination of past projects of the exact nature.
Estimation of labor requirements by defined project phases.
Adjustments based on working seasons.
Evaluation of local employment economic conditions.
Some companies call this “Scenario Planning for Disruption.”
Construction work is prone to many interruptions. Efficient employee administration should take care of the following:
Weather phenomena: Scheduling plans must be mobile and able to move assignments easily to tasks that can be undertaken indoors.
Supply chains: Scheduling plans must allow some workers to do something else should the ordered materials not arrive in time.
Illness and absenteeism: Keeping a good mouse of competent temporary staff or subcontractors who can do the work within a limited time.
Passing new laws: Instant reporting of compliance with new legislation is necessary when legislation changes.
Artificial Intelligence and Predictive Analytics
One of the most sophisticated forms of predicting people who one expects to look after is being part of AI-powered predictive staffing models that depend heavily on a project’s outcomes, features, location, and everything else that involves history.
With travel distance, necessary certifications, and personal productivity habits considered, AI scheduling assistants can optimize worker allocation.
Proactive workforce management solutions can analyze historical workforce data and discern behavioral patterns that can predict potential project delays.
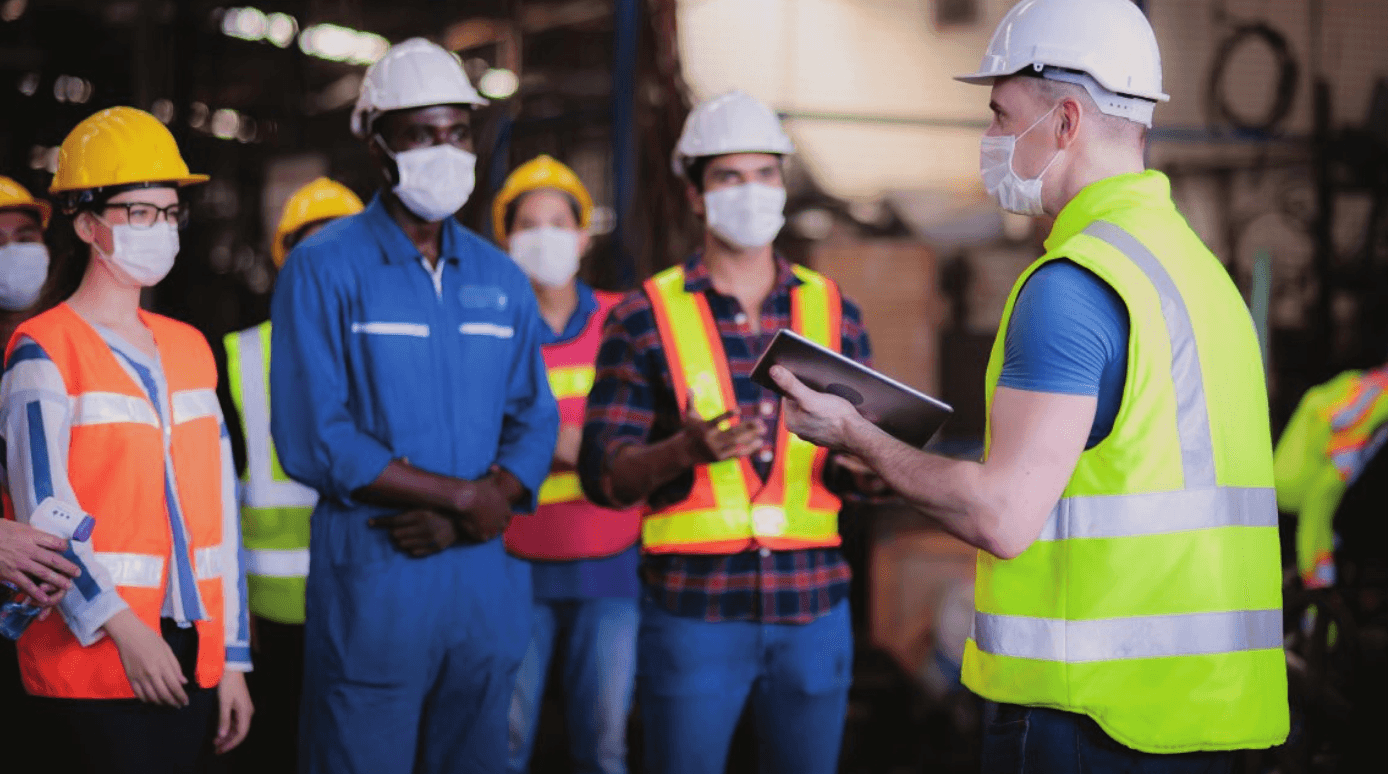
Technology Solutions in Workforce Management
Workforce Management Software Overview
The construction workforce management software market has matured significantly, with solutions now offering:
Feature Category | Key Capabilities |
Scheduling | Real-time adjustments, conflict detection, certification verification |
Time & Attendance | Mobile clock-in/out, geofencing, biometric verification |
Performance Tracking | Productivity metrics, quality assessments, milestone tracking |
Compliance Management | Certification tracking, safety training verification, regulatory reporting |
Communication | In-app messaging, document sharing, emergency notifications |
Leading platforms include Procore's Labor Management, Connecteam, Sitemate, and specialized construction modules from enterprise solutions like Workday and SAP.
Tools for Scheduling and Allocating Resources in Real Time
Modern scheduling tools are now integrated with mobile devices and have featured improvements like:
Mobile applications that allow employees to check their schedules and submit time off or shift day requests.
API integration with weather forecasting services for automatic schedule changes.
Allowing schedules to be assigned provided there is real-time verification of the required certifications and qualifications.
Calculating optimal crew compositions is possible according to tasks that need to be done and the available employees.
Travel times and site locations are tracked to reduce the time lost during transitions that do not contribute to productivity.
Technologies for Monitoring Safety and Compliance
Safety measures in the construction business is advancing due to technology through:
Smart helmets, vests worn by workers, and badges capable of monitoring workers' location, detecting falls, and measuring environmental risks are examples of wearable technology.
Computer vision systems, AI or artificial intelligence-powered surveillance, can identify safety breaches like lack of PPE and other unsafe activities.
Automatic checks of employee documents and their custom-defined report generation is known as digital compliance management.
Applying algorithms to identify potential incidents is known as predictive safety analytics.
Best Practices for Construction Labor Management
Programs for Training and Skill Improvements
Skill gaps are being closed by leading construction firms with these solutions:
Filling learning gaps with instructional materials delivered through mobile devices that workers can complete during downtime.
Simulating realistic scenarios that involve high risks is done without putting workers in danger using cross-training VR training.
Versatility across multiple construction disciplines is developed through cross-training programs.
Every employee can be mentored to aid with knowledge transfer from a more seasoned worker to a newcomer.
Support for certifications such as reimbursement for tuition costs or time off with pay to pursue additional training or education.
Implementing Competitive Benefits
Due to the limited number of willing workers, construction companies are improving their benefits as follows:
Offering a salary that pays a true wage for skills and the area’s cost of living.
Providing specific health and wellness services designed for workers in construction.
Establishing a clear and defined pathway for promotion and career progression.
Policies promoting work and family life balance, including guaranteed schedules when feasible.
Employee recognition for accomplishing safety, quality, and productivity goals.
Improving Team Communication and Collaboration
Managing a workforce effectively requires optimal communication:
Mobile toolbox talks that deliver the same safety messaging to every job site
Real-time collaboration applications that link office personnel with field employees
Transparent visual project management boards that display project priority and status
Structured feedback loops that capture workers’ suggestions on processes
Well-defined troubleshooting procedures for issues reducing the productivity of the workforce
Workforce Management Trends in Construction
The Intersection of IoT and Wearable Technology
Workplace management using the Internet of Things (IoT) is being done with:
Smart PPE that monitors vital signs, environmental conditions, and worker localization.
Equipment sensors that record usage patterns and operator actions.
Construction operations digital twins creation monitoring networks.
Automated RFID & Bluetooth check-in/check-out systems.
Cautioning environmental monitoring marks workers in dangerous conditions.
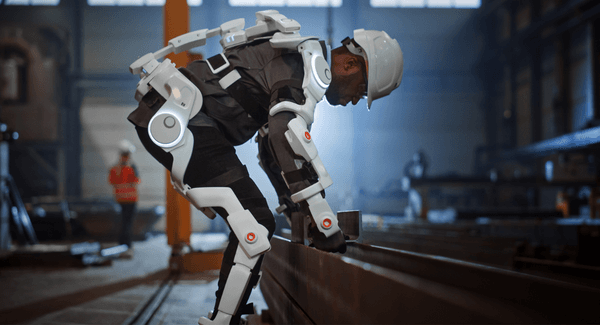
Artificial Intelligence and Machine Learning Take Over
Artificial intelligence takes the lead in developing advanced workforce management:
Stronger predictive staffing algorithms that expect labor with greater accuracy.
Voice documentation and reports using natural language processing.
Computer vision monitoring work quality and safety compliance supervision.
Tailored productivity insights dashboards for each worker
Workforce allocation optimization without limits through autonomous scheduling
Green and Sustainable Workforce Strategies
The integration of environmental awareness has transformed workforce management into a multi-dimensional domain through:
Advanced and simplified scheduling that reduces travel and equipment usage.
Development of green skills that address issues of sustainable construction.
Zoom-friendly positions are available for jobs that do not require a physical presence.
Elimination of paper documents and conversion to digital documentation.
Teaching the Circular economy, which focuses on material reuse and waste reduction.
Conclusion
The evolution of construction workforce management reflects a change from mechanical scheduling to an intricate strategic activity that accomplishes project objectives. To succeed in skill shortages, safety needs, and technology issues, businesses must adopt comprehensive workforce data planning, devote resources to modern technology, and build facilities that foster employee advancement.
Construction firms are better placed in this perplexed environment when overcoming current challenges or positioning themselves for a sustained competitive advantage by following the instructions in this guide. The remaining challenge and paradox of construction workforce management is to engage the human mind in thoughtful system building and to blend technology into designs that facilitate productivity and worker satisfaction.
FAQ
What is construction workforce management?
Construction workforce management is a systematic approach to planning, scheduling, tracking, and optimizing labor resources throughout construction projects. It encompasses everything from initial staffing forecasts and skill allocation to real-time scheduling adjustments, performance monitoring, and compliance management.
How does workforce management improve construction projects?
Effective workforce management improves construction projects by ensuring the right workers with appropriate skills are assigned to the right tasks at the right time. This optimization reduces labor costs, minimizes delays, improves quality, enhances safety compliance, and increases project profitability. Studies show that properly managed projects can reduce labor costs by 10-15% while improving on-time completion rates by up to 35%.
What are the common challenges in construction workforce management?
The most pressing challenges include industry-wide labor shortages (with an estimated 650,000 additional workers needed annually), an aging workforce (41% retiring by 2031), safety compliance complexities, skill gaps, scheduling inefficiencies, communication barriers between office and field, and difficulties in tracking productivity across multiple job sites.
How can technology enhance workforce management in construction?
Technology enhances construction workforce management through specialized software platforms that integrate scheduling, time tracking, and compliance functions; mobile apps that improve field communication and documentation; IoT devices and wearables that monitor safety and productivity; AI and predictive analytics that optimize resource allocation; and digital training tools that accelerate skill development.
What future trends are expected in construction workforce management?
Key future trends include increased adoption of AI-powered scheduling and forecasting, expansion of IoT and wearable technology for safety and productivity monitoring, greater emphasis on sustainability in workforce practices, more sophisticated predictive analytics for project planning, enhanced remote collaboration tools, and the integration of augmented reality for on-site training and task guidance.