Picture this: You're walking through a multi-story building that looks perfect from the outside, but the concrete on the first floor is already showing cracks. The fix? Tearing down everything above and starting over. That's a nightmare scenario that costs millions and could have been prevented with proper quality control.
In the US construction industry, quality control isn't just a nice-to-have—it's the difference between project success and catastrophic failure. Whether you're a contractor, project manager, or building owner, understanding quality control can save you time, money, and headaches down the road.
What Exactly Is Construction Quality Control?
Quality control (QC) in construction is your safety net during the building process. It's the systematic checking, testing, and monitoring of materials and workmanship to ensure everything meets specified standards and building codes.

Think of it as having a vigilant inspector who catches problems before they become expensive disasters. While quality assurance (QA) focuses on planning and preventing issues, quality control is about detecting and fixing problems as they happen.
Quality Assurance vs. Quality Control: Know the Difference
Many people use QA and QC interchangeably, but they serve different purposes:
Quality Assurance (QA) is proactive. It's about setting up processes and standards before construction begins. QA involves:
Project planning and design reviews
Establishing quality standards and procedures
Creating inspection schedules
Training personnel on quality requirements
Quality Control (QC) is reactive. It's about checking work as it happens.
QC includes:
Material testing and inspections
Monitoring construction activities
Identifying defects and non-compliance
Ensuring corrections are made immediately
Here's something important: On any given project, you can't do both QA and QC. That would create a conflict of interest. QA typically represents the owner's interests, while QC represents the contractor's quality monitoring efforts.
Why Quality Control Matters More Than You Think
Even though quality control services typically cost less than 1% of a construction budget, they can have a massive impact on your project's success. Here's why:
Financial Protection
Finding a bad batch of concrete early in construction might cost a few thousand dollars to replace. Finding it after you've built three floors on top of it? That's a multi-million dollar problem. Quality control catches these issues when they're still manageable.
Safety Compliance
Poor quality control can lead to life safety issues. When people live or work in buildings with substandard materials or construction, the consequences can be severe. Quality control ensures compliance with international building codes and local municipality requirements.
Timeline Management
Quality control helps maintain project schedules by catching problems early. When defects are identified and corrected immediately, projects stay on track. Waiting until the end of construction to address quality issues can cause significant delays.
How Quality Control Works in Practice
Effective quality control involves several key activities:
Material Testing
Every material that goes into your project needs testing. This includes:
Concrete strength testing
Steel quality verification
Soil compaction testing
Aggregate testing for proper gradation
Ongoing Monitoring
Quality control doesn't happen once—it's continuous.
Quality control teams monitor:
Daily construction activities
Material deliveries and storage
Workmanship standards
Environmental conditions affecting construction
Rapid Response
When problems are identified, quality control teams notify contractors or clients within 24 hours. This immediate communication allows for quick corrective action, preventing small issues from becoming major problems.
Pre-Construction Inspections
Quality control can even extend tofabrication shops before materials arrive on site. This proactive approach saves time and money by identifying problems before products are shipped to the job site.
The Quality Control Process: Step by Step
Here's how quality control typically works on a construction project:
1. Early Engagement
Quality control starts early, often during the planning phase. If the same company performed geotechnical engineering, they can build efficiencies into the quality control process.
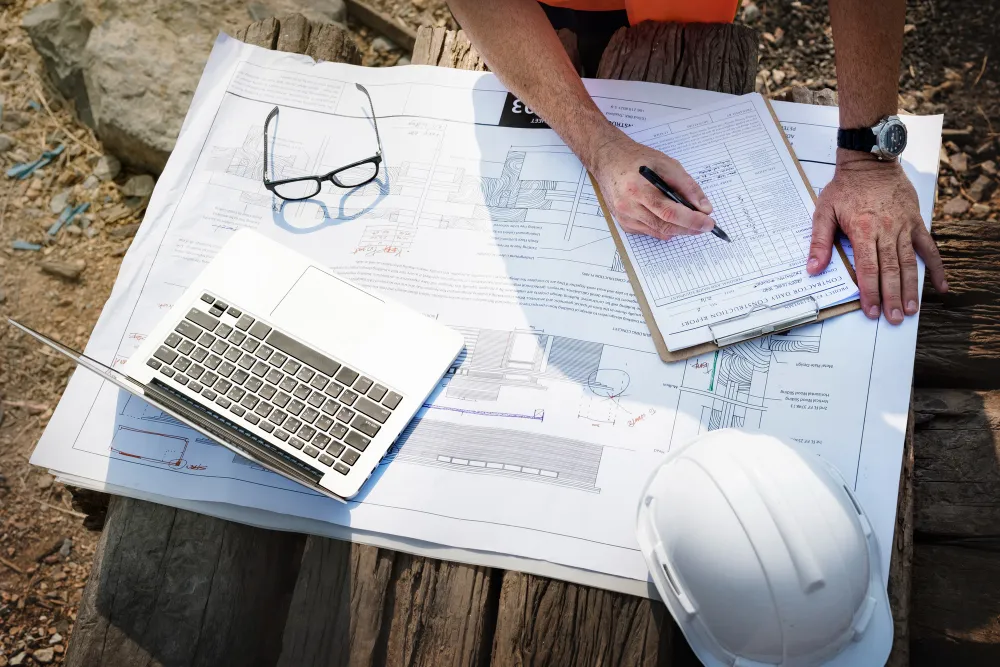
2. Plan Review
Quality control professionals review construction plans and specifications to understand project requirements and identify potential quality challenges.
3. Testing and Inspection Schedule
A comprehensive schedule is created that outlines when and what testing will occur throughout the project.
4. Real-Time Monitoring
As construction progresses, quality control teams conduct inspections, perform tests, and monitor compliance with specifications.
5. Documentation and Reporting
All quality control activities are documented, creating a record of compliance and any corrective actions taken.
6. Special Inspections
Many municipalities require specific inspections for certain construction elements. Quality control teams ensure these requirements are met.
Common Quality Control Challenges
Resource Constraints
Some contractors view quality control as an unnecessary expense. However, the cost of poor quality far exceeds the investment in proper quality control.
Communication Gaps
Poor communication between quality control teams and construction crews can lead to missed defects or delayed corrections.
Regulatory Complexity
Different municipalities have varying requirements for inspections and testing. Quality control teams must understand local regulations in each market.
Schedule Pressure
When projects are behind schedule, there's often pressure to skip or rush quality control activities. This is exactly when quality control becomes most important.
Best Practices for Effective Quality Control
Start Early
Begin quality control planning during the design phase. Early engagement allows for better integration of quality requirements into the construction process.
Maintain Independence
Quality control professionals should have the authority to stop work when quality issues are identified, regardless of schedule pressures.
Document Everything
Comprehensive documentation protects all parties and provides evidence of compliance with specifications and regulations.
Train Your Team
Everyone on the construction team should understand quality requirements and their role in maintaining standards.
Use Technology
Modern quality control incorporates digital tools for tracking, reporting, and communicating quality information in real-time.
The Bottom Line
Quality control in construction isn't just about checking boxes—it's about protecting your investment, ensuring safety, and delivering projects that meet or exceed expectations. While it might seem like an additional cost, effective quality control actually saves money by preventing costly rework and ensuring projects are completed on time and within budget.
Remember, this might be one of only a few projects you work on this year, but quality control professionals work on hundreds of projects. They've seen every problem that can come up and know how to prevent them.
Whether you're building a single-family home or a high-rise office building, quality control is your insurance policy against the unexpected. It's the difference between a project that succeeds and one that becomes a cautionary tale.
Don't let your next project become the leaning tower of your city. Invest in proper quality control from day one, and build with confidence knowing that every aspect of your project meets the highest standards of quality and safety.
Frequently Asked Questions
What is the difference between QA and QC in construction?
QA (Quality Assurance) prevents defects through planning and processes before construction. QC (Quality Control) catches and fixes problems through testing and inspections during construction.
Who is responsible for quality control in construction?
Either the contractor handles QC internally, or the owner hires an independent QC firm. QA and QC roles must be separate to avoid conflicts of interest.
What does a quality control inspector do in construction?
They test materials, conduct inspections, monitor construction activities, document compliance, identify defects, and ensure corrective actions are completed.
How much does construction quality control cost?
Quality control services typically cost less than 1% of the total construction budget but save money by preventing costly rework and delays.
What are the most common quality control tests in construction?
Common tests include concrete strength testing, soil compaction, steel quality verification, aggregate gradation, and asphalt density testing.
When should quality control start in a construction project?
Quality control should begin during the planning and design phase, before any construction work starts on-site.
What happens if quality control finds defects?
The QC team notifies the contractor within 24 hours, work may be stopped, and corrective actions must be implemented before continuing.
Is quality control required by law?
Most municipalities require certain inspections and testing to comply with building codes. Requirements vary by location and project type.
Can the same company do both design and quality control?
No, this creates a conflict of interest. QC must be independent of design and construction to maintain objectivity.
How long does quality control testing take?
Testing times vary—some tests give immediate results while others (like concrete strength tests) can take up to 28 days.
Ready to Implement Quality Control on Your Next Project?
Quality control isn't just about compliance—it's about protecting your investment and ensuring project success. Whether you're planning a residential development or a commercial high-rise, having the right quality control strategy can save you time, money, and stress.
Take Action Today:
Contact a Quality Control Professional: Get a consultation to understand your project's specific QC requirements
Review Your Current Processes: Evaluate whether your existing quality measures are adequate for your project scope
Plan Early: Don't wait until construction starts—begin quality control planning during the design phase
Train Your Team: Ensure everyone understands their role in maintaining quality standards
Need Expert Quality Control Services? Connect with certified quality control professionals who understand local building codes and have experience with projects like yours. Don't let poor quality control turn your dream project into a nightmare.
Start building better today. Your future self (and your budget) will thank you.