Bottom Line Up Front: Successful construction cost management ensures you deliver projects for less than your estimated costs. This involves accurate estimating (calculating true project costs) and rigorous cost control (delivering within budget). Master these two processes, and you'll transform project losses into consistent profits.
Every construction project manager has been there – watching a promising project slowly bleed money while desperately trying to figure out where it all went wrong. You started with a solid estimate, won the bid, and felt confident about profitability. Then reality hit: material costs spiked, productivity dropped, and unexpected issues emerged.
Here's the harsh truth: construction cost management isn't just about crunching numbers – it's about survival. With profit margins often razor-thin and competition fierce, the difference between successful contractors and those going out of business often comes down to one critical skill: managing costs effectively throughout the entire project lifecycle.
What Is Construction Cost Management?
Construction cost management is about ensuring the planned costs are less than the actual costs. In simple terms, if you're a construction business owner or work for a construction contractor, your goal is to secure a project at a profitable price, estimate costs correctly, and then deliver the project for less than your estimate to generate profit.
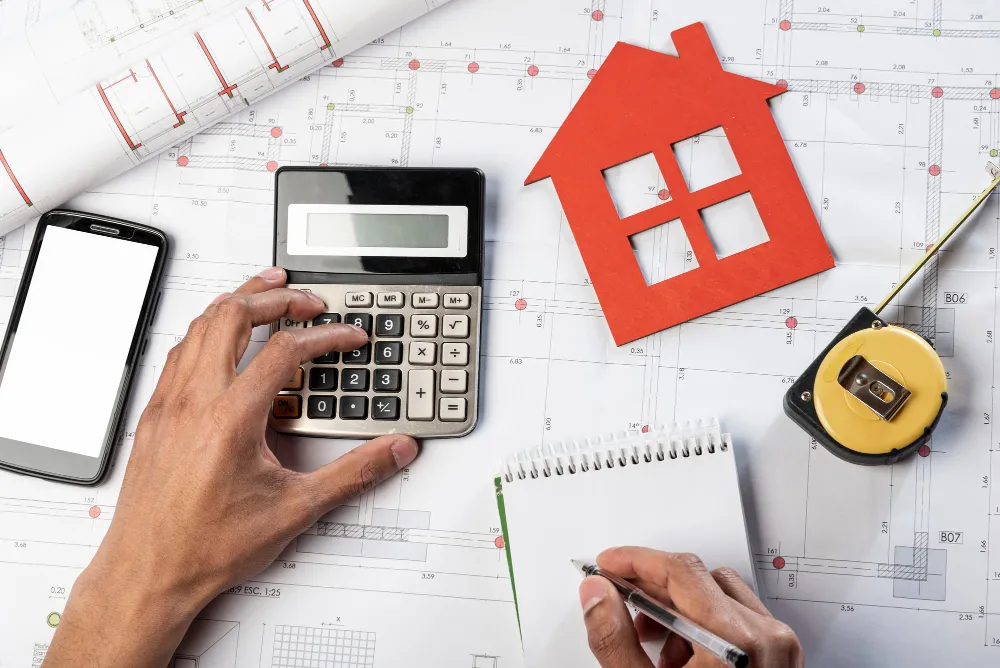
This process breaks down into two essential components:
Estimate costs: Accurately calculating how much something will cost to complete
Monitor and control costs: Delivering the project for less than your budget during execution
Think of it as a two-stage rocket. First, you need accurate fuel calculations (estimating). Then, you need precise navigation and efficient fuel consumption (cost control) to reach your destination profitably.
Understanding Project Cost Components
Before diving into cost management strategies, you need to understand what makes up project costs:
Direct Costs
These are the costs of completing physical construction works.
Each direct cost item consists of:
Labor: The workforce needed to complete tasks
Plant/Equipment: Concrete pumps, excavators, and other machinery
Materials: Concrete, reinforcement, formwork, etc.
Subcontract costs: Specialized services like crane operations
Indirect Costs
These are the costs to manage and supervise the works, broken into:
Non-recurring indirect costs: One-time expenses like site setup
Recurring indirect costs: Ongoing expenses like project manager salaries, temporary fencing, and security
The Estimating Process: Building Your Financial Foundation
Step 1: Create a Work Breakdown Structure
Decompose your project scope into component pieces. Create a comprehensive list of every single activity needed to complete the project. This systematic approach ensures nothing gets overlooked.
Step 2: Complete Quantity Takeoffs
For each activity, determine key quantities. For a concrete foundation, you'll need square meters of formwork, tons of reinforcement required, total volume of concrete, and surface area calculations.
Step 3: Calculate Direct and Indirect Costs
Determine plant, labor, materials, and subcontract costs for each activity. Then calculate your recurring costs (based on project duration) and non-recurring costs (one-time expenses).
Step 4: Add Risk, Contingency, and Profit
Work out uncertain events or conditions that could impact costs and make allowances (contingency). Then apply your profit margin – the markup that ensures your business remains viable.
Cost Control: Turning Estimates into Profits
Once you've won the project, your goal shifts to delivering the project for less than your estimated costs.
Pre-construction Cost Control
Budget Creation: Transform your estimate into a working budget. The way you calculate costs differs from how you'll track expenditure. For example, estimators might calculate PPE costs at $2 per work hour, but during execution, you need a lump sum PPE budget to track against.
Design Management: If you're responsible for design development, manage the process to ensure what you're specifying can be built within your estimate. Avoid scope creep by preventing the addition of unnecessary, costly features.
Strategic Procurement: Run competitive procurement processes to find high-quality subcontractors and suppliers at optimal prices. This single activity can make or break project profitability.
Construction Cost Control
Efficient Resource Management: Plan and coordinate works effectively to avoid delays and maintain productivity. If your estimate assumed 50 meters of trenching per day, achieve that productivity or better through efficient resource utilization.
Cost Monitoring: Track every dollar spent and match it to work completed. Set up comprehensive cost tracking systems using tools like Earned Value Management to identify cost overruns early when you can still take corrective action.
Change Management: Effectively manage changes to ensure you're not doing additional work without compensation. Understand your contract scope boundaries and claim entitlements for client-caused delays or requested changes.
Earned Value Management: Your Project Performance Dashboard
Earned Value Management (EVM) integrates schedule, cost, and scope to measure project performance. It's like having a real-time financial dashboard for your project.
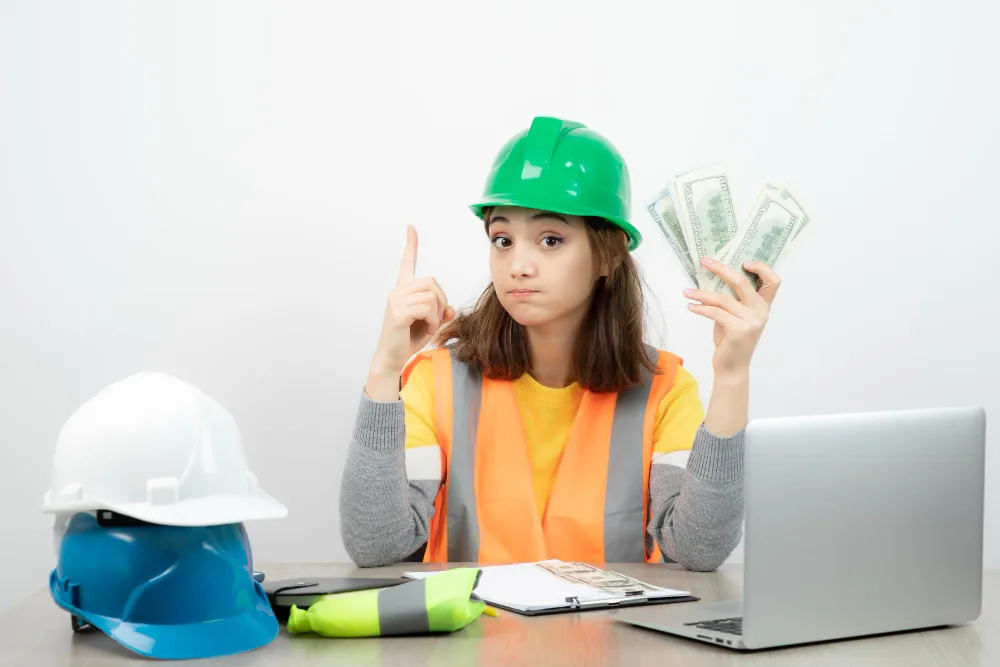
The Three Key Metrics:
Planned Value (PV): The budgeted cost of work forecasted to be completed at a given time – what you planned to spend based on your schedule.
Actual Cost (AC): The actual cost of works completed – what you've actually spent to date.
Earned Value (EV): The budgeted cost of work completed – what amount of your budget you've "earned" through completed work.
Variance Analysis:
Schedule Variance (SV) = Earned Value - Planned Value tells you if you're ahead or behind schedule in dollar terms.
Cost Variance (CV) = Earned Value - Actual Cost reveals if you're over or under budget for the work completed.
These calculations provide objective, quantitative indicators of project performance, allowing you to make data-driven decisions rather than relying on gut feelings.
Common Cost Management Pitfalls and Solutions
Poor Initial Estimates: Invest in detailed quantity takeoffs and use historical data from similar projects. Regularly update your cost databases with actual project performance data.
Inadequate Change Management: Establish clear change order processes and train your team to identify and document changes immediately. Don't perform extra work without approved change orders.
Weak Cost Tracking: Implement daily cost tracking systems and weekly variance analysis. Use technology to automate data collection where possible.
Design Scope Creep: Establish design freeze dates and change control procedures. Regularly review design decisions against budget constraints.
The Path to Consistent Profitability
Construction cost management requires discipline, systematic processes, and continuous improvement. The most successful contractors treat cost management as a core competency, not an afterthought. They invest in training, technology, and processes that enable accurate estimating and tight cost control.
Remember, every dollar saved on a project flows directly to your bottom line. In an industry where 5-10% profit margins are considered good, effective cost management can be the difference between thriving and merely surviving.
Frequently Asked Questions
Q: How often should I update cost projections?
A: Weekly for active projects, with detailed monthly reviews including variance analysis.
Q: What's the biggest factor in cost overruns?
A: Poor change management, followed by inaccurate productivity assumptions and inadequate cost tracking.
Q: How can I improve estimating accuracy?
A: Maintain detailed historical cost databases and conduct thorough post-project reviews.
Q: What percentage should I allow for contingency?
A: Typically 5-15% depending on project complexity and risk factors.
Q: How do I handle cost overruns mid-project?
A: Immediately identify the source, assess impact, develop recovery plans, and communicate transparently.
Q: What's the difference between budget and estimate?
A: An estimate calculates costs; a budget is a tool for tracking and managing expenditure during execution.
Q: When should I implement Earned Value Management?
A: For projects over $1M or complex projects where schedule and cost performance are critical.
Q: How can technology help with cost management?
A: Use project management software for real-time cost tracking, mobile apps for field data collection, and analytics tools for variance analysis.
Successful construction cost management isn't magic – it's a systematic approach to planning, monitoring, and controlling project finances. Master these fundamentals, and you'll build a foundation for sustainable profitability in your construction business.