For contractors, managing expenses is always a juggling act. In the construction industry, labor is one of the top three expenses alongside materials and equipment, typically costing between 30 and 50 percent. As we move into 2025, it’s clear that understanding construction labor costs is critical for any project’s success and revenue. Obtaining this information can be helpful for construction company owners, project managers, or any professionals in the field, as it details the many aspects of labor costs, how they are calculated, and potential ways to minimize expenses.
Here, you will find the most useful and relevant information on estimating construction labor costs, staffing costs associated with hiring, the use of staffing agencies, and other important and relevant changes that will occur in the industry in the next few years.
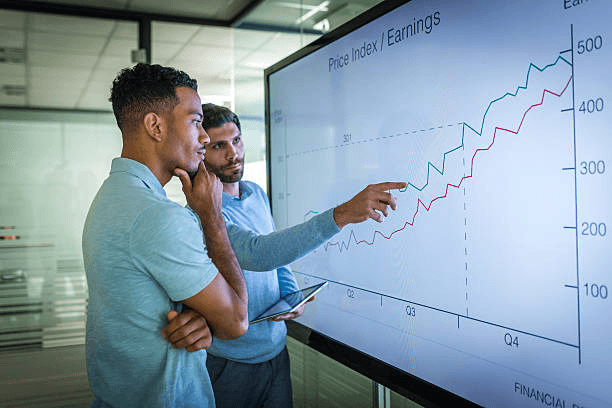
Factors Influencing Construction Labor Cost
Any estimation of construction labor costs needs to consider several vital aspects that will impact each unique project differently. Knowing these factors is imperative for constructing a sensible budget.
Geographic Location and Its Impact
The site has a major impact on the cost of construction labor. The Federal Bureau of Labor Statistics explication indicates that construction labor costs differ across various locations in the United States by as much as 40%.
Urban Areas Relative to Rural Ones: Urban Areas Relative to Rural Ones: Urban centers have a greater demand for construction services, but these areas tend to have higher living costs and command higher labor rates. For example, construction workers in New York City earn more than 35% above the national average.
Regional Economic Conditions: Areas with developed economies like California and Massachusetts, likely have higher rates of labor to regions like Mississippi or Arkansas with lower living costs.
Local Regulations and Requirements: Unionized areas where there are added compliance measures associated with building codes and permit requirements are likely to incur higher labor costs because of the added wage standards.
Accessibility and Logistics: Sites that are remote or hard to reach may incur higher total labor costs because of the need to attract qualified laborers, and premium wages need to be drawn.
Skill Level and Experience Required
The level of detail and expertise needed to complete a construction project correlates with the labor cost of the same project.
Specialized Trades: The general laborer is, on average, paid less than the specialized plumbers, electricians, and HVAC specialists. According to the Construction Labor Research Council, specialized tradespeople can earn 25-75% more than unskilled workers.
Experience Premium: It's common for individuals with more experience to earn 30 to 50 percent higher than those just entering the field, which is an outcome of their experience and quality of work.
Certifications And Licensing: Additional certificates or diplomas (for instance, welding certificates or master electrician dockets) demand higher wages as they offer specialised expertise and legal qualifications.
Projected Expenses: Some skilled trades with increased difficulty require more complex projects, which in turn lead to payment issues but with reduced chances of poor work and other subsequent challenges.
Economic Factors In And External To The Market
The economy tends to have the greatest impact on construction labor expenses.
Tighter Labor Markets: In 2025, competition for recruits continues as the construction industry faces a shortage. The Associated Builders and Contractors has reported a nationwide shortfall of about 500,000 skilled workers. Because many companies are vying for a limited pool of workers, salaries rapidly escalate.
Overall Economic Inflation Effect: General inflationary tendencies have raised construction employee salaries by an average of 4.2 percent each year over the past two years, which is higher than several other sectors.
Seasons: In regions where construction is seasonal, peak building months tend to surge in expenses due to increased demand.
Other Sectors: Certain industries, such as manufacturing and energy, when growing, are capable of drawing workers away from construction, creating upward pressure on wages.
How to Calculate Construction Labor Cost
Accurate labor cost estimation is fundamental to project success and profitability. Here's a structured approach to calculating these costs effectively.
Step-by-Step Labor Cost Estimation
Define the Essential Labor Positions: List the classification types associated with trades necessary to complete the project Figure out the amount of skill needed to perform each job Indicate the amount of employees required for each classification
Set the Pay Rate per Hour: Determine the average pricing for various trades within the area you are working at Consider the wage payment mandates, if any exist, that need to be fulfilled Consider the payment margins for overtime hours, work done on holidays, or weekends
Estimate the Number of Working Hours: Allocate parts of the project to be worked on individually Decide on the amount of time you expect will go into accomplishing each activity Estimate productivity levels considering working circumstances and how difficult the project is
Figure the Direct Cost for Labor: Take the hourly payment, multiply that by the expected time for each labor category, and add them all together Combine the total payments, which results in the estimated expense for labor
Incorporate Labor Cost Overhead: Determine the taxes that you will have to pay for salaries (generally 10-15 percent of the salary) Include expenses for covering workers’ compensation insurance (it depends on the trade and location) Include payments covering other employee options such as health insurance and pensions
Account for Other Costings: Allocate other expenses on top of normal costings (normally a 5-15 percent margin) dependent how complex and risky the project is Account for probable material supply delays, bad weather, and other things that might make working difficult
Tools and Calculators for Accurate Estimation
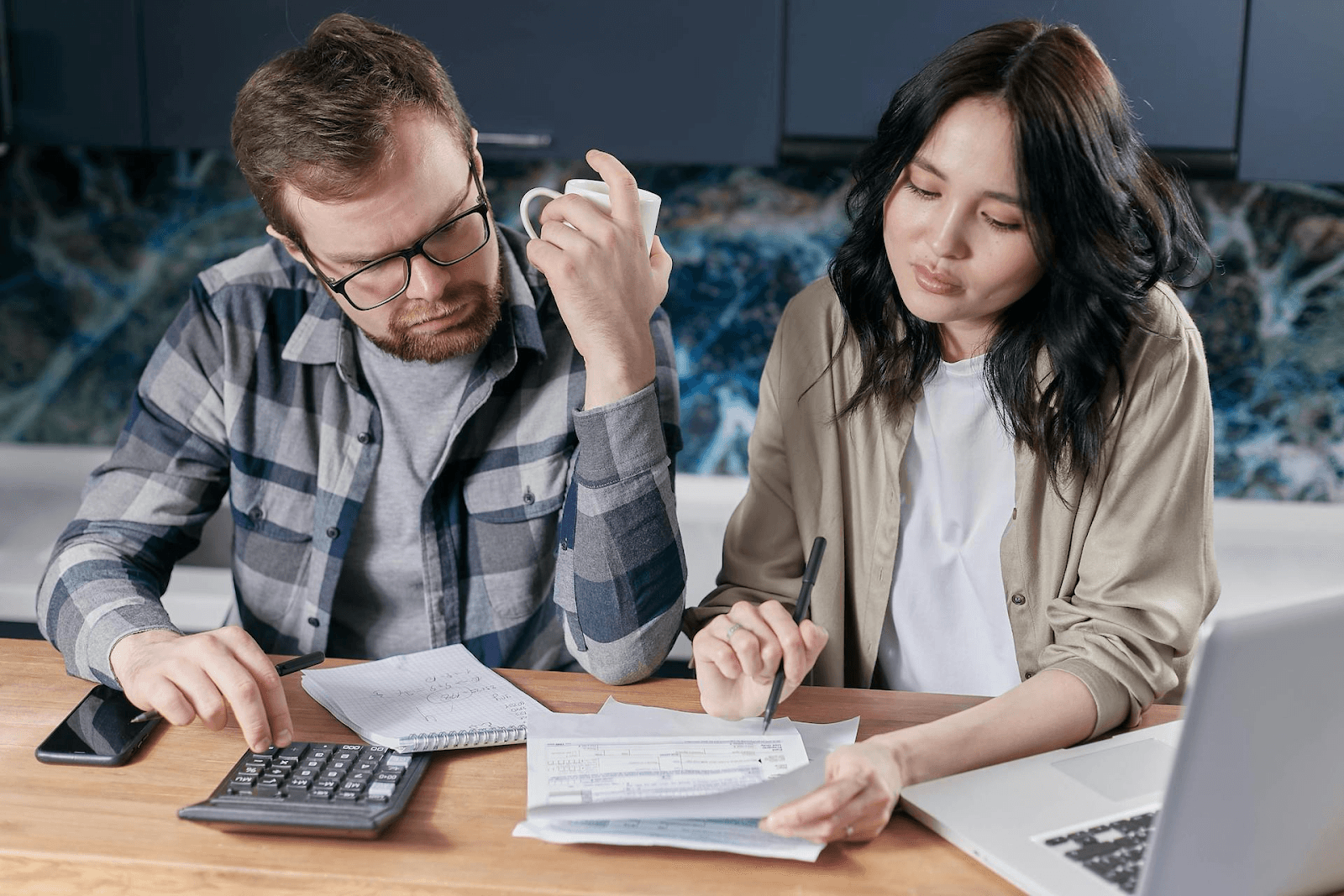
Here are the some Labor Estimation tools that can be used:
- Construction Estimation Software: Several digital platforms estimate and assess productivity for construction builds. ProEst, STACK, and Buildxact provide an integrated software that pairs together large databases of labor rates and productivity.
- Industry-Specific Databases: These can serve as dependable benchmarks. Resources such as RSMeans give updated labor cost information relevant to region and specialty.
- Mobile Applications: Field-based applications enable real-time tracking of labor costs, enabling refinement estimates to be based on actual performance. Allowable performance tracking is enhanced, and estimating is to be continuous.
- AI-Powered Estimation Tools: Newly developed artificial intelligence software successfully predicts labor requirements through historical estimation data analysis. As with every project, they learn and are ideal at improving their estimates over time.
Recruitment Cost Savings in Construction
With labor shortages continuing to challenge the construction industry in 2025, optimizing recruitment processes offers significant cost-saving opportunities.
Strategies to Minimize Recruitment Costs
1. Foster Enterprise Brand Recognition:
- Emphasize safety records and employee retention rates. Reduce employee turnover and promote loyalty.
- Use social media to build up your industry presence and market yourself to passive candidates.
2. Create Online Reputation Management Referral Programs:
- Implement tiered incentive plans for referrals who stay for certain durations.
- Honor employees who make several quality referrals.
3. Collaborate with Schools and Colleges:
- Offer apprenticeship and internship opportunities.
- Get involved in career days at colleges and industry conferences.
4. Enhance Online Recruiting Sites:
- Use automated tracking for easier candidate processing.
- Employ targeted adverts to attract specific people.
5. Keep and Maintain Employees:
- Define career progression to be as clear as possible.
- Multiple Training programs and certification options.
Benefits of Efficient Recruitment Processes
There are many more benefits to cost-saving strategies aside from savings:
Lower Time-to-Hire: The less time there is to fill a role, the less likely there will be project delays and overtime spending. Organizations with good recruitment strategies have been noted to hire within an average of 30-40% of the time it would normally take.
Better Quality of Candidates: Attracting high caliber candidates during the recruitment phase reduces training costs and improves productivity. Better-matched hires are 2.5 times more likely to stay in the company for 2 years or more.
Lower Turnover Rates: Repetitive hiring and replacing new employees can cost a lot of money, so employers are more careful about making hiring decisions. It is estimated that replacing an experienced construction employee costs in between 50-150% of their yearly pay.
Better Project Continuity: Reduces erosion of knowledge and energy previously invested in accomplishing goals, which enables less skilled workers to complete tasks more efficiently, leading to a 15-25% increase in productivity.
Improved Team Cohesion: Few communication problems, and safety improvements tell us that better working relationships are formed over time at the crew level.
Case Studies: Successful Recruitment Cost Reduction
Case Study 1: A Contractor Goes Through Digital Transformation
A medium-sized commercial contractor located in the Southwestern region decreased recruitment expenses by 35 percent because of:
Using an AI-automated applicant tracking system
Changing the design of the career page to mobile friendly
Issuing a formal employee referral program
Partnering with three local vocational schools
Among the benefits were reducing average time-to-hire from 45 days to 18 days and decreasing first year turnover by 40%.
Case Study 2: Builder Seeks to Improve Employee Retention
One residential building company located in the Northwest had primary focus on retention in the captured region, implementing:
A comprehensive skills training program
Establishing a promotion ladder
Providing profit sharing
Allowing some employees to have flexible schedules
Their approach decreased annual turnover from 32% to 14%. This saved these companies around 320,000 dollars annually on recruitment costs, with the companies fully staffed throughout the tight labor market.
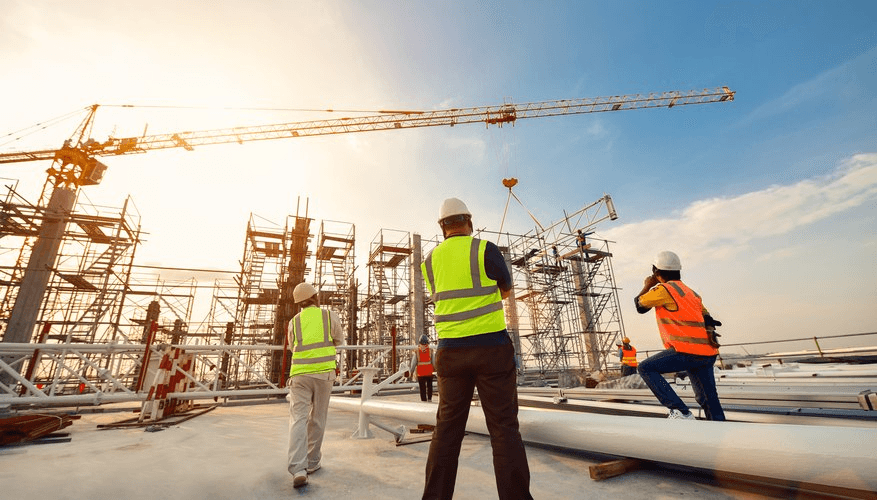
Trends and Insights for 2025
The construction labor landscape continues to evolve rapidly. These current trends will shape labor costs and availability through 2025 and beyond.
Emerging Trends in Construction Labor Cost
Accelerated wage increases in specialized trades: Electricians, plumbers, and HVAC technicians receive annual wage increases of five to seven percent, compared to general construction labor which is only three to four percent.
Increased regional divergence: High-growth regions are experiencing economic stagnation, which causes a regional disparity in labor cost. These areas are seeing wage inflation two to three times as high as economically stagnant areas.
Expansion of benefits- Companies are beginning to offer richer health care benefits, paid vacations, and retirement contributions to compete for employees. This shift denotes a change in competition from wages to benefits.
Implications of an aging workforce- Companies are offering exorbitant salaries between fifteen to twenty-five percent above market value to help ease the burden of having to retrain new senior-level employees after veteran workers retire.
Effect of immigration policy- Stricter borders have resulted in wage increases due to lack of available workers in these regions, especially for states that would usually depend on immigrant workers.
Technological Advancements Influencing Labor Costs
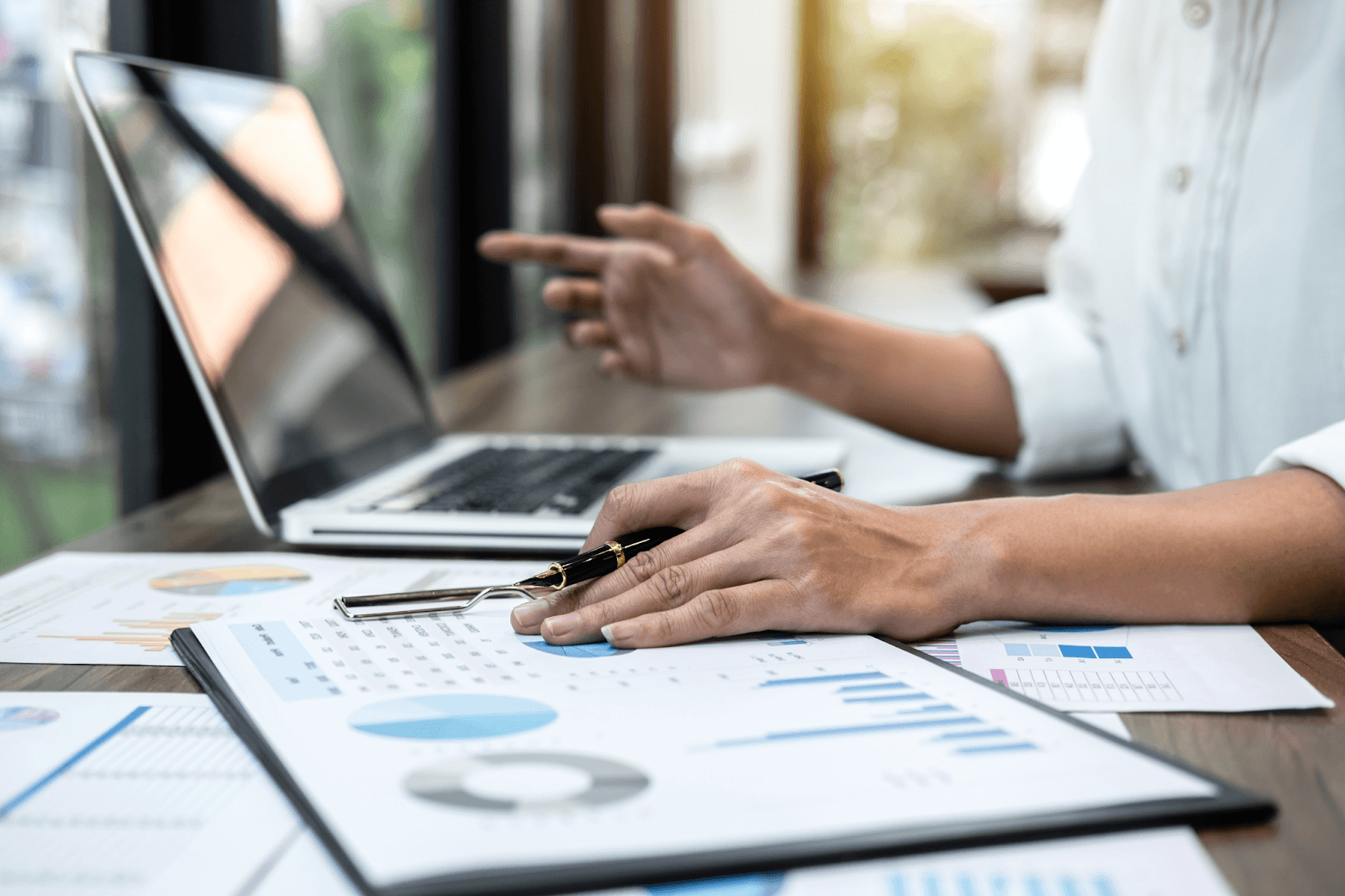
Technology is reshaping labor requirements and costs across the construction sector:
Prefabrication and Modular Construction: Off-site construction methods reduce on-site labor hours by 20-40% for applicable project components, shifting labor needs from field workers to factory settings.
Robotics and Automation: Automated equipment for tasks like bricklaying, concrete finishing, and rebar tying is reducing labor requirements for specific tasks while creating demand for technologically skilled operators.
Exoskeletons and Wearable Technology: These innovations extend workers' careers by reducing physical strain, potentially expanding the labor pool by enabling older workers to remain productive longer.
Remote Work for Support Functions: Design, estimation, and project management roles increasingly incorporate remote work components, expanding the talent pool beyond local markets and potentially reducing compensation requirements.
Digital Collaboration Tools: Advanced project management platforms reduce coordination time and miscommunication, improving overall labor productivity by an estimated 15-20%.
Future Predictions and Preparations
Taking sociological changes and economic growth indicators into consideration, construction companies should anticipate the following changes:
Persistent Workforce Gaps: It seems that a shortage of adequately skilled employees will linger on for the next 5 years, with The Associated Builders and Contractors expecting an annual deficit of 546 thousand workers to fulfill infrastructure demands.
Growing Specialization Premiums: There appears to be a gap between the wages of non-specialized and specialized workers that is only projected to increase, with estimates reaching a staggering 100 to even 150 percent for the most sought out skillsets.
Workers with Technology: Contractors who wish to succeed will focus more on investing in technology that enhances employee productivity as opposed to increasing the amount of labor available to them.
Blended Staffing Strategies: Companies will adjust the ratio of full-time permanent staff, temporary staff from agencies, and subcontractors based upon the requirements of the project and the prevailing economic conditions.
Enhanced Employment Training Programs: Firms that establish comprehensive training frameworks will be in a better position than their competitors in regard to hiring, retaining, and enhancing workforce productivity.
Conclusion
The labor costs related to construction have emerged for both difficulties and opportunities from an organizational perspective for 2025. Economic entities can remain competitive with construction projects with all active labor hitches by grasping the relevant circumstances driving such costs, executing strict estimation methods, optimizing selection procedures, utilizing staffing companies, and tracking new developments.
The most successful organizations will take the labor costs in their totality acknowledging that the cheapest option is not always best and investment in workers, their training, and retention pays the best dividends over time. The blend of conventional construction skill with other contemporary management practices will enable companies to manage the rising difficulty in the labor market.