Off-site construction is transforming how America builds in 2025. From housing to healthcare, developers and contractors are shifting toward smarter, faster, and safer methods. Off-site construction moves critical building work to controlled factory environments, drastically reducing delays, improving safety, and answering the labor shortage challenge. If you're a contractor chasing tighter timelines or a worker looking for a more stable environment, off-site construction isn't just an option anymore—it's the new standard.
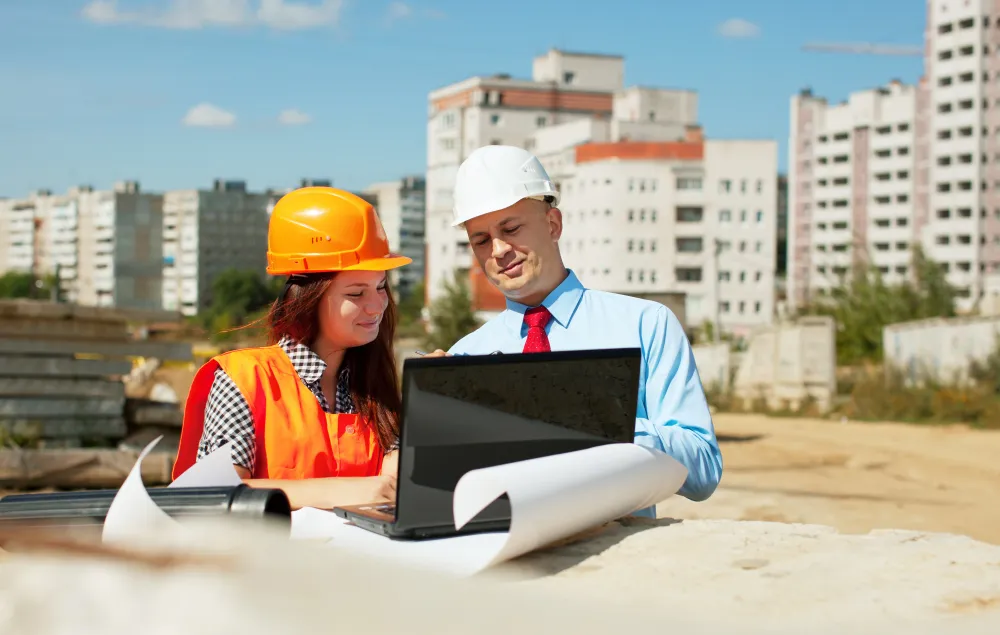
What Is Off-Site Construction?
Off-site construction refers to the practice of manufacturing building components away from the final build site and transporting them for on-site assembly. This includes:
Modular Units: Fully finished rooms or sections craned into place.
Panelized Systems: Wall, roof, and floor panels assembled quickly onsite.
Hybrid Builds: Combining site work with off-site mechanical pods, racks, or elevator cores.
Work happens inside climate-controlled factories with precision tools and no weather delays. Meanwhile, the site crew handles grading, utilities, and foundation prep—cutting total build time in half.
Why 2025 Is the Breakout Year
Off-site construction isn't new—but in 2025, it’s going mainstream. Here’s why:
Labor Shortages: The industry still lacks hundreds of thousands of skilled tradespeople. Off-site builds increase productivity by 30–40%.
Schedule Demands: Projects like data centers and warehouses require faster delivery. Off-site methods shave weeks or even months off timelines.
Higher Quality: Factory settings mean robotic welds, laser-precision layouts, and lower error rates.
Sustainability: Up to 60% less job site waste and fewer diesel trips to the site.
Tech Integration: Tools like BIM, digital twins, and IoT sensors now support real-time coordination and QC.
Major hospital networks, infrastructure projects, and developers now list off-site methods in RFPs as standard practice.
U.S. Regions Leading the Off-Site Surge
Some areas are going all-in on off-site:
Region | Why It’s Hot | Typical Projects |
Pacific Northwest | Tight codes + rainy weather | Prefab classrooms, timber schools |
Southeast & Texas | Population surge + land | Modular apartments, student housing |
Mountain West | Harsh winters, remote sites | Panelized hotels, utility buildings |
Mid-Atlantic & NE | Urban density, union cost | Pod bathrooms, MEP racks |
Even rural contractors are using modular solutions to avoid hiring large on-site teams.
Off-Site Construction Methods and Trends
1. Volumetric Modular
Entire rooms built in a factory—finished with flooring, MEP, and furnishings. Ideal for hotels, apartments, and dorms.
2. Panelized Systems
Walls and floors made from cross-laminated timber or steel arrive flat-packed and go up fast—great for customized designs.
3. Pods & MEP Racks
Standalone bathrooms or prefabricated mechanical units eliminate field coordination headaches.
4. Digital Fabrication
Robots, CNC machines, and AI-driven QC make sure every panel is accurate to the millimeter.
5. Green Construction
Reduced emissions, better waste control, and ESG-ready builds attract investors and community approval.
Explore how construction technology is enabling this transformation.
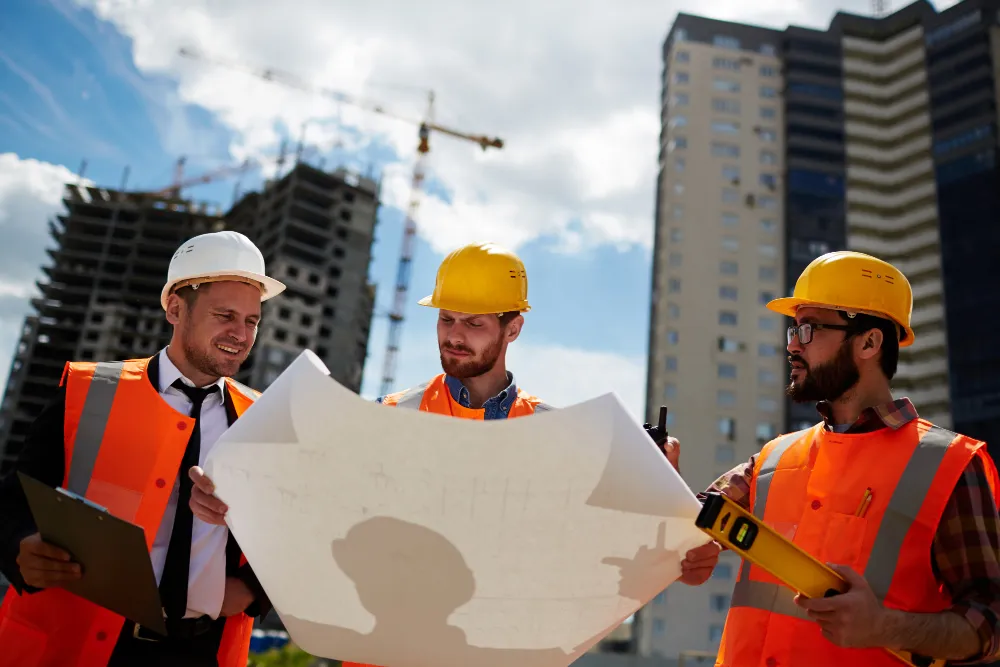
Why It Matters for Builders and Developers
Cash Flow: Finish faster, bill sooner, and lower financing costs.
Predictability: Weather and no-show subs don’t slow down the factory.
Risk Management: Lock in pricing with factory contracts.
Site Logistics: Fewer deliveries, smaller crews, less congestion.
Reputation: Faster, greener builds win bids and community support.
Career Opportunities in Off-Site Construction
This isn't about machines replacing workers—it’s about smarter work:
Factory Trades: Indoor work for carpenters, welders, electricians.
Installation Crews: Specialize in crane rigging and modular assembly.
Digital Operators: BIM techs and robotics coordinators ensure precision.
Logistics Leads: Manage module shipping, crane scheduling, and site staging.
As off-site expands, so does demand for workers ready to pivot into these high-value roles.
How to Plan Your First Off-Site Project
Evaluate Repetition: Projects with repeated rooms or layouts = big ROI.
Start Early: Engage off-site providers during schematic design.
Align Teams: Make sure owners, lenders, and inspectors understand modular workflows.
Pre-Plan Site Logistics: Think about access routes, crane picks, and staging areas before production begins.
Start Small: Begin with prefab bathrooms or MEP racks, then scale up.
Conclusion
Off-site construction is no longer experimental—it’s essential. With faster timelines, higher precision, and fewer labor headaches, builders who adopt off-site now are winning more jobs and delivering better results. And for workers, it opens doors to modern roles with year-round work, better safety, and new tech.
This is the construction of the future—and it’s already happening.
FAQs
Is off-site construction more expensive?
Not necessarily. Upfront costs may rise, but savings on time, waste, and labor usually make up for it.
Are modular buildings up to code?
Yes. Modules meet the same building codes and inspections as site-built structures.
Do off-site methods limit design options?
No. While modular cores are standard, exteriors and layouts can be fully customized.
What about transporting large units?
Most modules fall within permitted size ranges. For larger ones, logistics teams manage permits and routes.
Who warranties the work?
Manufacturers cover factory work; GCs cover site assembly. Clear contracts avoid confusion.