Construction sites are inherently hazardous environments where workers face numerous risks daily, from heavy machinery and elevated work areas to electrical hazards and exposure to harmful substances. Ensuring the safety of workers is not only a legal obligation but also a moral one.
A strong emphasis on safety helps protect workers from injuries, reduces project delays, and enhances overall productivity. Safety training plays a pivotal role in minimising these risks, equipping workers with the knowledge and skills to navigate their daily tasks safely.
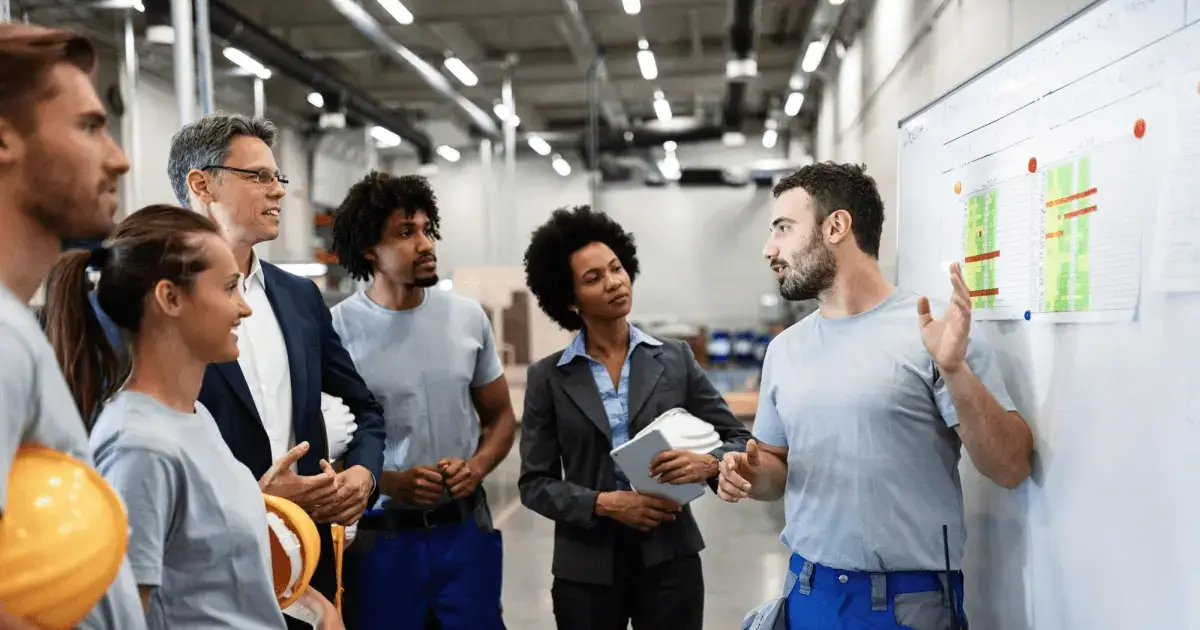
Introduction to commitment to safety training for all workers
Safety is a top priority, and providing comprehensive safety training to all workers is imperative. By ensuring employees are well-prepared and equipped to handle potential hazards, we can create a secure work environment for everyone.
Safety training programs should be tailored to meet industry standards and comply with both federal and state regulations, demonstrating a commitment to protect our workforce and maintain a safe worksite.
Why Safety Training is Crucial for Construction Workers
High-Risk Environment of Construction Sites
Common hazards encountered on construction sites
Construction workers face various hazards that can pose severe risks to their health and safety. These include falls from heights, accidents involving heavy machinery, exposure to harmful chemicals, and risks of electrical shock or fire.
Additionally, workers often operate in high-stress environments with tight deadlines, which can further elevate the risk of accidents. Training is essential to help workers recognize and avoid these hazards, ensuring that safety measures are effectively implemented.
Statistics on workplace injuries and fatalities in the construction industry in the U.S.
According to the Occupational Safety and Health Administration (OSHA), the construction industry accounts for nearly one in five workplace fatalities in the U.S. each year.
In 2020 alone, there were approximately 1,008 fatalities, with falls, struck-by incidents, electrocutions, and caught-in-between accidents being the leading causes. These statistics highlight the need for stringent safety protocols and thorough training programs to mitigate the risks faced by construction workers.
Reducing Accidents and Preventing Injuries
The role of safety training in minimising workplace accidents
Safety training is a critical tool in reducing workplace accidents by equipping workers with the skills and knowledge to navigate their environment safely.
Through training, workers learn about hazard recognition, safe work practices, and emergency response protocols, which collectively contribute to a safer worksite.
By instilling a culture of safety, companies can significantly reduce the likelihood of accidents and foster an environment where workers feel secure.
Benefits of training in terms of reducing injury rates and related costs
Effective safety training not only protects workers but also reduces the financial burden on companies. Fewer accidents result in lower medical expenses, decreased workers' compensation claims, and reduced downtime due to injuries.
Moreover, a strong safety record enhances a company’s reputation and can lead to better business opportunities and insurance premiums. Investing in safety training ultimately leads to long-term savings and improved worker morale and productivity.
Key Components of Effective Safety Training
Hazard Identification and Assessment
Importance of training workers to recognize potential hazards
Teaching workers how to identify potential hazards is the first step in preventing accidents. Workers who are trained to recognize risks, such as unstable scaffolding, electrical hazards, or improperly stored materials, are better equipped to report or address these issues before they result in accidents.
Hazard recognition empowers employees to proactively participate in maintaining a safe worksite.
Methods for conducting hazard assessments
Hazard assessments involve systematic examinations of the worksite to identify and evaluate risks. These can be conducted through routine site inspections, safety audits, and job safety analyses (JSAs).
Training workers on these methods ensures they understand how to spot and address hazards specific to their roles and the construction site layout.
Use of Personal Protective Equipment (PPE)
Overview of essential PPE for construction workers
Personal Protective Equipment (PPE) is essential in safeguarding workers from injuries. Common PPE for construction workers includes hard hats, gloves, safety goggles, steel-toe boots, and high-visibility vests.
Depending on the specific tasks, additional PPE such as respirators, ear protection, and fall arrest systems may be required.
Training on proper usage and maintenance of PPE
Providing PPE is not enough; workers must also be trained in its proper usage and maintenance. This includes ensuring a correct fit, understanding how to inspect equipment for wear and tear, and knowing when to replace it.
Properly maintained PPE is vital for worker protection, and training ensures that it remains effective throughout its use.
Emergency Procedures and First Aid
Emergency response protocols and evacuation procedures
Training workers in emergency response protocols is essential for minimising harm during incidents such as fires, chemical spills, or severe weather. Workers should be familiar with evacuation routes, assembly points, and communication procedures.
This knowledge enables swift and organised responses, reducing panic and confusion during emergencies.
First aid training to provide immediate assistance in case of injury
In a high-risk environment like a construction site, having workers trained in first aid can be life-saving. First aid training includes basic skills like CPR, wound care, and recognizing signs of severe injuries.
Quick first aid response can stabilise injured workers until professional medical help arrives, reducing the severity of injuries and improving recovery outcomes.
Safe Equipment Handling and Operation
Training on the correct use and handling of machinery and tools
Construction work often involves the use of heavy machinery and specialised tools, which can be dangerous if mishandled. Training programs should cover the safe operation of equipment such as cranes, forklifts, and power tools, including how to perform pre-use inspections and follow operational guidelines.
Proper equipment handling reduces the risk of injuries associated with machinery misuse.
Importance of regular equipment inspections and maintenance
Regular inspections and maintenance of equipment are critical for preventing malfunctions that could lead to accidents. Training workers to conduct routine checks ensures that equipment is safe and in good working condition.
This proactive approach helps prevent accidents caused by equipment failure and contributes to a safer overall worksite.
Regulatory Requirements for Safety Training in Ohio
OSHA Standards and Regulations
Overview of OSHA regulations relevant to construction safety
The Occupational Safety and Health Administration (OSHA) establishes safety regulations to protect workers across various industries, with specific provisions for construction due to its high-risk nature.
OSHA mandates that construction companies implement safety measures and provide training to help workers understand and comply with safety protocols.
These regulations cover a range of safety issues, including fall protection, hazard communication, and the use of personal protective equipment (PPE).
Specific training requirements mandated by OSHA for construction workers
Under OSHA’s regulations, construction workers must receive training on several critical topics, such as hazard recognition, fall protection, and safe equipment handling. OSHA also requires specific training on confined spaces, trenching and excavation, and scaffolding safety.
Additionally, workers must be trained to use PPE properly, and employers are responsible for ensuring that training is conducted in a language and format that employees can easily understand.
By meeting OSHA’s training requirements, construction companies not only comply with federal law but also create a safer environment for their workers.
State-Specific Guidelines for Ohio
Ohio's construction safety regulations and additional requirements
Ohio enforces both federal OSHA standards and state-specific regulations to ensure safe construction practices. The Ohio Bureau of Workers’ Compensation (BWC) requires construction employers to implement safety programs that address specific hazards relevant to their operations.
Employers must maintain records of all safety training sessions, which can be requested during inspections by state or federal agencies. Ohio also mandates specific safety training for certain types of construction work, such as those involving heavy machinery or hazardous materials.
Compliance with Ohio's Department of Health and Department of Labor standards
In addition to OSHA standards, construction companies in Ohio must comply with regulations set by the Ohio Department of Health and the Ohio Department of Labor.
These regulations may include requirements for reporting workplace injuries and illnesses, providing specific types of PPE, and adhering to safety protocols for hazardous substances.
Ohio state agencies often work in conjunction with OSHA to conduct inspections and ensure compliance, helping to protect workers and reduce workplace incidents.
Benefits of Comprehensive Safety Training Programs
Enhanced Worker Confidence and Productivity
How safety training improves workers' confidence on-site
When workers receive thorough safety training, they gain confidence in their ability to perform their tasks safely. This confidence stems from knowing that they are prepared to handle potential hazards and equipped with the skills to respond effectively in emergencies.
Trained workers are more likely to feel secure on the job, which can reduce anxiety and improve focus.
Impact of safety on productivity and overall worksite efficiency
A well-trained workforce is a productive workforce. Safety training minimises the occurrence of accidents, which in turn reduces downtime and disruptions to the workflow. Workers who feel safe are more likely to work efficiently, contributing to overall project progress and ensuring that deadlines are met.
By investing in safety training, companies not only protect their workers but also enhance operational efficiency and project success.
Strengthened Reputation and Client Trust
The importance of safety for company reputation and client satisfaction
Safety is a key factor that clients consider when choosing a construction partner. A strong safety record reflects a company’s commitment to its workers and projects, enhancing its reputation in the industry.
Clients are more likely to trust a company with a proven track record of prioritising safety, as it indicates professionalism, reliability, and a reduced risk of delays due to accidents.
Safety training as a factor in securing future projects and investments
A company that invests in safety training demonstrates a proactive approach to risk management, which can be attractive to investors and clients. A solid safety program can make a company more competitive when bidding for new projects, as it shows a commitment to protecting workers and delivering high-quality results.
Additionally, companies that prioritise safety are more likely to receive positive reviews and referrals, leading to more business opportunities in the future.
Reduced Costs and Liability
Lowering insurance costs and reducing legal liability through training
Effective safety training can lead to significant financial savings for construction companies. By reducing the likelihood of workplace injuries, companies can lower their insurance premiums and minimise the cost of workers’ compensation claims.
A strong safety program also reduces the risk of legal action, as companies are less likely to face lawsuits related to workplace accidents when they can demonstrate compliance with safety regulations.
Financial benefits of fewer accidents and safer practices
Fewer accidents mean less time lost to injuries and less expenditure on medical treatments, repairs, and compensations. Safe practices also prevent costly delays and enable projects to be completed on time and within budget.
By investing in safety training, companies not only protect their workforce but also save money and improve their bottom line. In the long run, a commitment to safety can lead to greater financial stability and a more resilient business.
Bottomline
Safety training is not just a regulatory requirement; it is a crucial aspect of maintaining a secure worksite and protecting the well-being of our employees. In the high-risk construction industry, investing in safety training helps prevent accidents, reduces costs, and fosters a culture of responsibility and care.
We remain steadfast in our commitment to worker safety and regulatory compliance. We recognize that our employees are our greatest asset, and we are dedicated to providing them with the tools, training, and support they need to stay safe on the job.
By prioritising safety, we not only safeguard our workers but also build trust with our clients, partners, and the communities we serve. Together, we strive to set new standards for safety in construction and continue to lead by example.