When it comes to construction work, safety is not just a priority; it is a necessity. A thoughtfully crafted construction safety plan could be the difference between a successful undertaking and an expensive catastrophe.
This guide walks through the key elements of an effective safety plan, from creating checklists and assigning trained personnel to conducting hazard assessments. It also covers how to align with OSHA standards and updated industry practices for 2025. Let’s break down how to keep your site and crew safe with a plan that meets today’s demands.
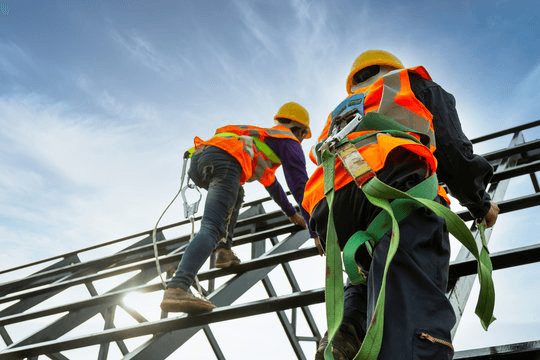
Understanding construction safety plans
What is, in its simplest form, a construction safety plan? It is a comprehensive document with policies and procedures detailing all the measures needed to protect workers, equipment, and the construction site’s surroundings. It is designed with the intention to clearly identify probable dangers, decrease the risks, along with offering a framework to respond effectively to emergencies.
Construction remains one of the most hazardous industries, with over 1,000 worker fatalities reported each year, according to the U.S. Bureau of Labor Statistics. That’s why a safety plan isn’t just a formality—it’s a critical part of protecting lives on-site. From identifying risks early to setting clear procedures, a strong safety plan can prevent accidents and keep the entire crew safer throughout the project.
The Value of an Effective Safety Plan
What motivates businesses to use man-hours to draw up a safety plan? Here is why:
Increased Productivity: Reduced employee injuries translate to lost time due to work interruptions.
Legal Compliance: Under legal regulations such as OSHA, compliance means businesses are not exposed to penalties and civil litigations.
Reduced Expenses: Fewer incidents will increase insurance coverage, reduce downtime, and waste.
Increased Productivity: Work morale is positively influenced by prioritized workplace safety standards.
Key Takeaway: In construction, the life safety plan should ensure all pre-construction activities and safety requirements are completed beyond compliance for every pre-construction interval, such as deadlines.
Important Elements of a Construction Safety Plan
Checklist For Safety Construction Site Inspections
An employee's safety checklist form is the first level of defense that can be done by anyone. Here are the details:
Labor Protective Equipment (LPE): LPE includes working pants and coats, LPE vests, shirts, LPE hard hats, gloves, cardiac pads, and goggles.
Mobile Site Inspections: Constant supervision of scaffold and electrical safety, and fall prevention.
Emergency Protocols: Clearly identifiable exits, first aid supplies, and extinguishing equipment.
Machinery Safety: Heavy equipment is properly guarded and maintained.
Consider the possibilities of IoT devices for real-time site condition monitoring–smart sensors notifying teams of possible structural vulnerabilities or adverse weather conditions.
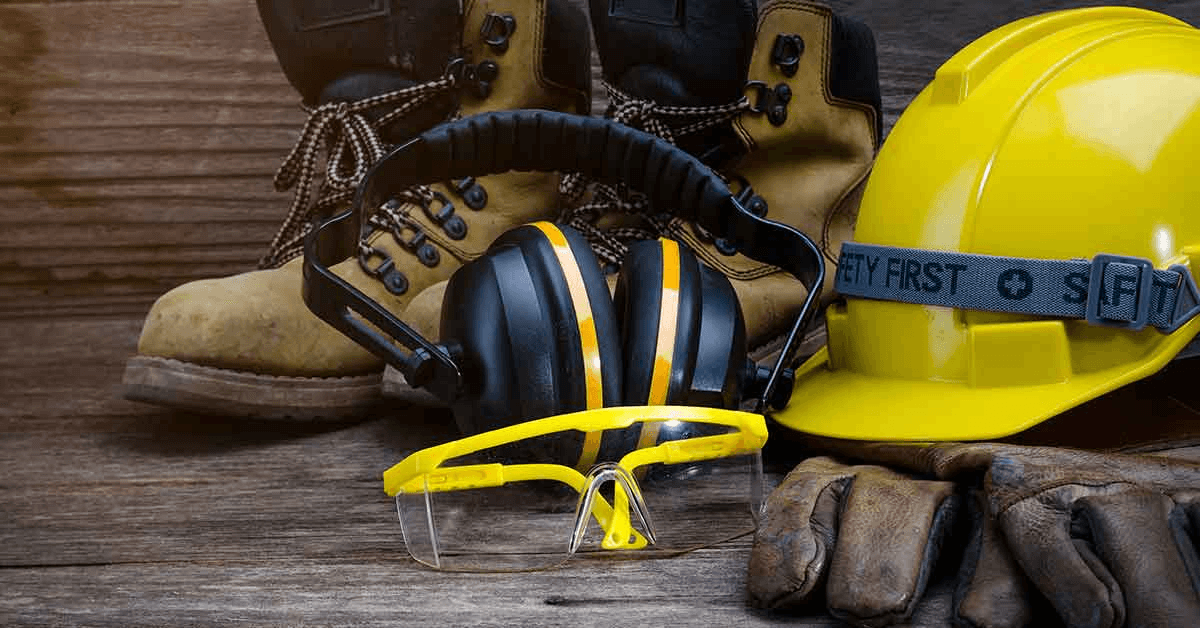
Hazard Identification and Risk Assessment
Assessment of workplace hazards in a systematic manner is the backbone of workplace safety. This process entails:
Raising Fingers: Mark unprotected edges, spaces that are too crowded, proximity to chemicals, and confined spaces as possible threats.
Evaluating Impact: Every hazard has a likelihood of occurrence and a level of severity; both need to be assessed.
Mitigation Controls: Barriers, training, and ventilation control the risks.
A 2023 OSHA report indicated that over 30 percent of construction sector deaths are caused by falls. AI and drone site surveying tools help identify risks, making it easier to avoid incidents, which is a breakthrough for tech companies.
Trained Construction Staffing
Your construction staff becomes a liability if the training provided to them is subpar. Trained construction staffing guarantees that every person understands their responsibilities in securing the site. This involves:
Safety Training: Instructional sessions on equipment operation, emergency action drills, and identification of potential hazards.
Certification: Validation of possession of OSHA 10 or 30-hour training.
Delegation: Appointment of compliance and update safety officers.
Key takeaway: The mix of technological solutions and human capital creates a safety net that is hard to compete with.
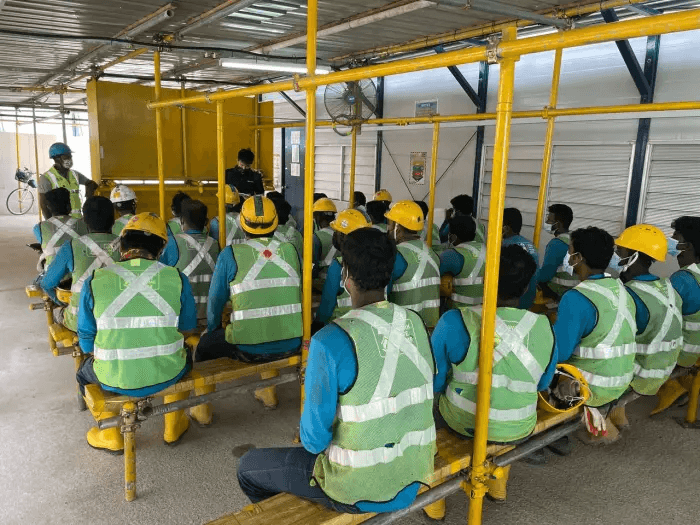
How to Develop a Construction Safety Plan
Step-by-Step Instructions
Do you need a working safety plan? Choose one of these action steps:
Evaluate the Site: Perform a site-specific walkthrough to capture all particular site-related risks.
Define Objectives: Establish specific safety objectives, such as a goal of zero lost time injuries.
Develop Rules: Set policies regarding the use and adequacy of PPE, reporting of incidents, response to emergencies, among others.
Create Construction Site Safety Checklists: Develop a project-specific construction site safety checklist.
Team Training: Properly train all employees in the area to the point that they ll be able to implement the safety measures.
Documentation: Store all training records such as inspection and incident records.
Ensure Routine Review: Change the strategy as the project progresses or as risks within the project shift.
Required Tools and Resources
Creating a safety plan doesn't have to be daunting. Make use of:
OSHA Guidelines: For a plan’s preliminary outline, check OSHA.gov for templates and compliance checklists.
Digital Tools: Real time safety tracking can be done using Procore, SafetyCulture, and Safety Reports.
Expert Consultation: Use specialized safety consultants to check the safety plan for gaps and omissions.
By constructing a safety plan tailored for specific age groups, construction companies can leverage AI-driven analytics to anticipate likely risks using historical data. For more information, read our article AI in Construction Safety.
Key Takeaway: Building a safety plan becomes easier with a well-defined plan and the right tools.
Safety Plans in Accordance with OSHA Policies
Is there a safety plan in place? Yes, for the greater part of construction work, especially ones with great risk. The basic requirements of OSHA include the following:
Safety Programs: A plan that aims at preventing potential dangers and site-specific contingencies.
Training: Basic safety training must be done for workers given a chance to face danger.
Documentation: A Detailed report of injuries, illnesses, and safety audits must be recorded.
In addition, stringent non-compliance could result in considerable fees Being OSHA breach fees can rise to $15,000 per breach as of 2025. Stay in the clear by making frequent visits to OSHA’s Construction Page.
Also, apart from OSHA, adopting industry alkaline practices goes a long way in differentiating you.
Self-initiated safety audits: Conduct safety audits in-house before the actual OSHA inspection.
Staff: Allow workers to report dangers without resentments or vengeance.
Applied science: Wearable technology which tracks workers' fatigue or temperature can provide aid.
Key takeaway: Losing money isn’t the aim; instead, it creates the need for a replaceable culture.
Effectively and routinely maintain a safety plan. Self-familiarize yourself with the report. Do not diverge from it.
A safety plan becomes useless when there is no one to manage it. Scenarios help prepare in the right measure.
Emergencies should be simulated in advance to gauge response readiness.
Rules of safety must be carefully and openly displayed for easy access.
Updating and Reviewing Safety Protocols
Construction sites change, and so should your safety plan. Quarterly reviews should be scheduled to:
Address New Hazards: Consider scope or equipment changes.
Change Procedures: Add insights gained from near-miss events or incidents.
Update Refresher Training: Ensure personnel are trained with the current materials in active use.
Final Insight: Safety plans, when managed dynamically, can respond to challenges and protect people over time.
Conclusion
The safety plan for construction must be detailed and tailored to fulfill every regulatory requirement, as it demonstrates commitment to the safety of the team and the business. Building a safer workplace requires addressing hazard identification, ensuring staffed positions are trained, and compliance with OSHA standards.
Don’t forget the plan; renew it often, and invest in training because the effort translates directly to fewer accidents, reduced costs, and a strengthened organizational reputation.
Frequently Asked Questions (FAQ)
1. What is a safety plan for construction?
A construction safety plan is a documented strategy that outlines measures to protect workers and the public on a construction site by identifying hazards, setting safety protocols, and ensuring compliance with regulations like OSHA.
2. How do you write a safety plan?
Start by assessing site-specific risks, defining safety goals, developing policies for hazard mitigation, creating checklists, training your team, documenting everything, and reviewing the plan regularly for updates.
3. How do I create an OSHA safety plan?
Follow OSHA guidelines by creating a written program addressing site hazards, providing training, maintaining records of incidents, and ensuring compliance with specific standards like fall protection or PPE requirements.
4. Does OSHA require a safety plan?
Yes, OSHA mandates safety plans for most construction projects, particularly those involving significant risks, to ensure worker protection and regulatory compliance.
5. What are the key components of a construction safety plan?
Essential elements include a construction site safety checklist, hazard identification and risk assessment, trained staffing, emergency protocols, and regular safety audits.