The struggle between reducing costs versus maximizing profits is a growing concern in the competitive construction industry today. It is a well-known fact that construction company owners face numerous challenges like the volatile material prices, inconsistent labor availability, and ever-growing regulatory requirements, while they still have to ensure quality and client satisfaction. In this guide, we shall provide you with actionable approaches for cost optimization and profit maximization along with operational transformation to elevate profits in 2025.
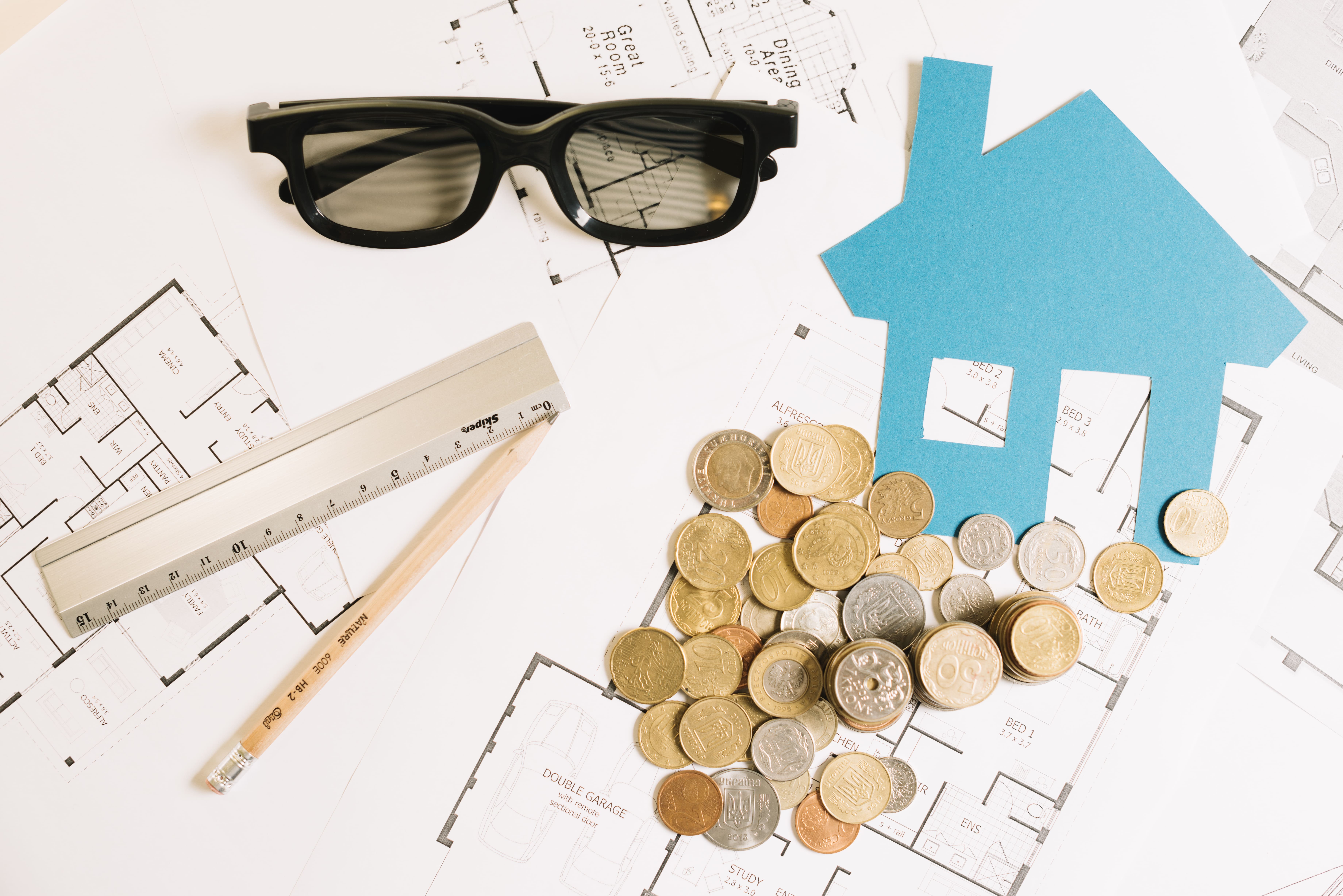
Understanding Cost Reduction vs Cost Optimization
Definitions and Differences
While these terms are pretty confusing and are sometimes used interchangeably, both cost reduction and cost optimization are different ways to improve financial health.
Cost reduction: This strategy focuses more on achieving desired financial targets by reducing operational expenditure. Outright eliminating staff, switching to cheaper materials, cutting certain services or trims can all cut costs strategically. Neglecting quality or efficiency standards usually backfires when an operational cost reduction approach is applied haphazardly.
Cost Optimisation: Cost optimization aims to justify expenditure. Imposing boundaries on spending without purpose can bring negative outcomes. Instead, focus on capturing as much value possible on every dollar spent. This could be investing in more efficient technologies or processes which may increase spending but pay off more in the long term.
As Mark Johnson, a construction economist at BuildEcon Institute, puts it: “The distinction is basic: cost reduction asks ‘how can we spend less?’ while cost optimization asks ‘how can we spend better?’”
Importance of Balancing Both for Construction Companies
- Balanced construction approaches are a hallmark of successful firms in contemporary markets, combining:
- Immediate operational cash inflow: Strategic cost reduction provides rapid financial relief.
- Long-term operational durability: Cost optimization maintains enduring competitiveness and quality.
- Versatility: Companies that excel at both can adapt to new conditions with speed.
As noted in a 2024 report by the Construction Financial Management Association, construction firms that employed a balanced approach to cost strategies experienced profit margins 23% higher than those who relied solely on aggressive cost-cutting measures.
Techniques to Cut Down on Construction Cost
Streamlining Processes and Project Management
In construction, wasteful processes hurt a lot. Here are some suggestions:
- Lean construction principles: Banish activities that do not add value, and concentrate on continuous workflow.
- Standardized procedures: Write specific and detailed instructions for performing routine tasks.
- Effective scheduling: Plan to reduce worker and equipment downtime to the bare minimum.
- Prefabrication opportunities: Evaluate if certain components can be assembled in controlled environments away from the job site.
Leveraging Technology and Automation
The incorporation of technology in the construction industry is regarded to be one of the most lucrative cost-cutting initiatives:
- Building Information Modeling (BIM): Decrease the need for rework by clash detection prior to the start of construction.
- Project management software: Enhance coordination and decrease administrative work burden.
- Drone surveys: Reduce the cost of surveying while enhancing the level of precision and safety.
- Automated equipment: Decrease labor cost for repetitive processes while enhancing accuracy.
According to a McKinsey report published in 2025, digitised construction firms incurred costs that were 15-20% lower than their unadapted counterparts.
Optimal Resource Allocation and Minimizing Waste
- The financial ramifications of a project can be hit hard by material waste and poor allocation of resources:
- Materials tracking systems: Help improve control of materials reducing loss or theft.
- Turn waste into revenue: Reduce disposal costs by recycling materials.
- Ensure fleet maintenance improves: Right size equipment fleets.
- Disposition of equipment should minimize waste.
Techniques for Maximizing Profit for Construction Companies
Pricing Approaches and Contracts
Your contracts and pricing structure has a great impact on profitability:
- Bidding strategically: Concentrating on the projects that bring greater profit rather than focusing on quantity.
- Value-based pricing: Pricing based on what is delivered, not on cost-plus formulas.
- Contract clause optimization – Escalation clauses for material price fluctuations.
- Managing change orders: Create clear guidelines for documenting and pricing alterations.
Improving Productivity and Efficiency
Directly boosting productivity leads to profit enhancement:
- Specialization – Reallocate business resources to focus on project types where your firm has demonstrated competitive efficiency.
- Skills training – Improving worker training programs to increase output quality and speed.
- Incentive programs – Modify compensation so employees are rewarded for productivity and quality.
Improvement Suggestions
Establishing a culture devoted to running improvement processes leads to continuous profit growth:
- Defining company KPIs or “Key Performance Indicators” for all operation functional units.
- Regular reviews – Performing post-project analyses and identifying improvement opportunities.
- Feedback loops for process improvements defined by frontline employees.
- Setting internal performance benchmarks for measuring against industry standards as well as competitors.
Successful Cost Reduction Examples
Horizon Builders – This mid-sized commercial contractor implemented a comprehensive waste reduction program that decreased their material costs by 12% in just six months.
Through the installation of material tracking software alongside waste elimination training, they financially benefited by over $450,000 annually for each of their projects.
Westfield Construction: In response to the ever-increasing fuel prices, this infrastructure contractor turned to fleet telematics and route optimization software. This advanced fuel and equipment maintenance cost tracking brought about a further 22% decrease, translating to roughly $380,000 in annual savings.
Profit Optimization Triumphs
Summit Contractors: Implementing value-based pricing for their design-build services enabled this residential builder to boost profits from 8% to 14% while remaining competitively priced. This feat was accomplished by better conveying the quality differentiators as well as the post-construction energy savings to their clients.
Metropolitan Builders: A commercial construction firm that adopted BIM technology and prefabrication capabilities reported completion of projects 30% faster than prior, alongside a 25% drop in change orders. Within the first year of implementation, they reported an 18% increase in profit margins.
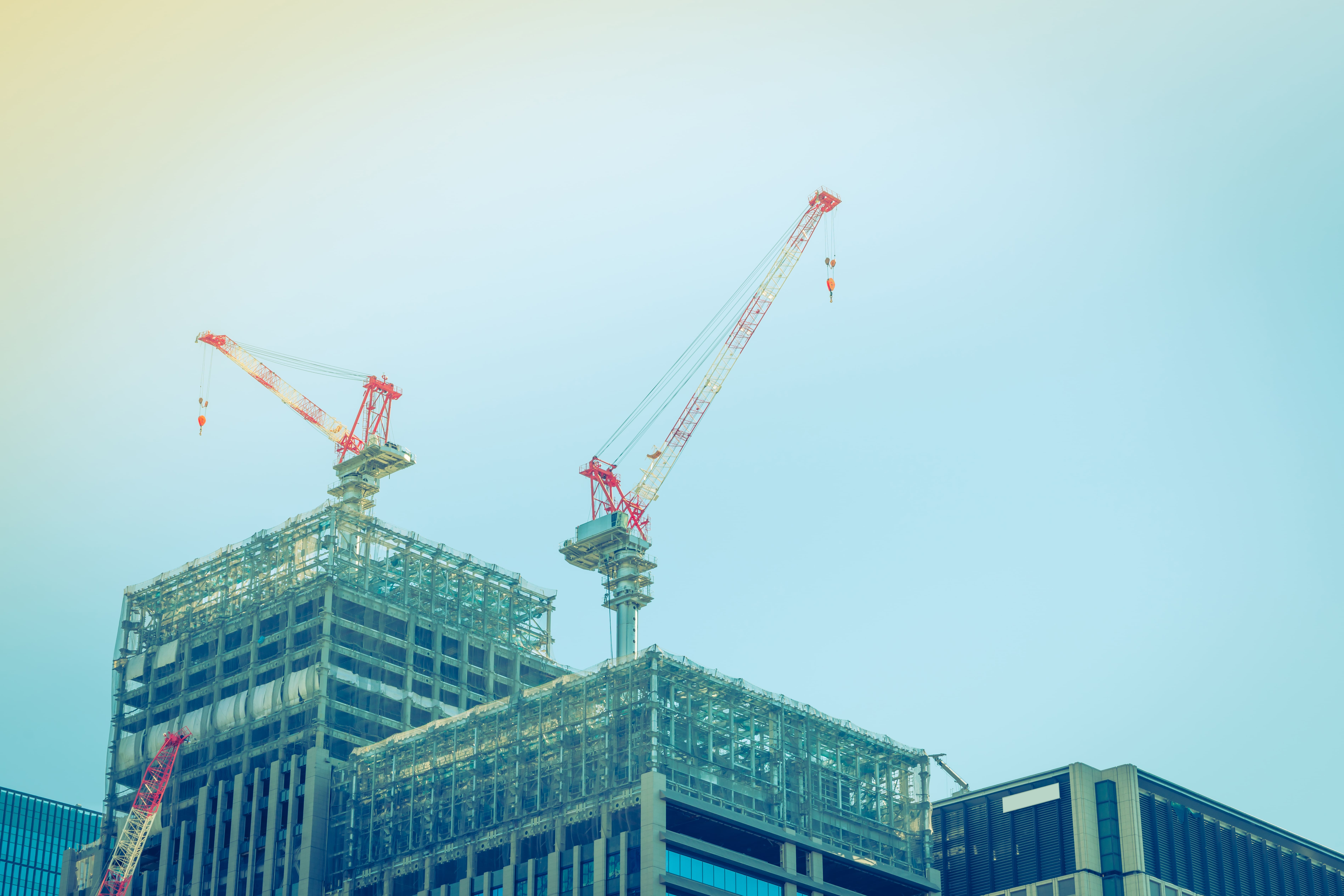
Tools and Technologies for Cost Reduction and Optimization
Software Solutions for Budgeting and Planning
Some technology solutions stand out for their use in construction cost management:
- Procore: Complete cost control alongside project management.
- Buildertrend: Advanced budget tracking for residential builders.
- PlanGrid: Work document management and collaboration to minimize communication issues.
- CoConstruct: Budgeting and estimating functions with a client communication platform.
Innovative Construction Technologies
These software not only enhances technologies, but also improves the construction industry's economics:
- 3D printing: Labor and material costs associated with intricate parts are being minimized.
- Modular construction: A reduction in on-site labor costs, while quality improves.
- Robotics: Repetitive tasks such as bricklaying and concrete finishing are now automated.
- Advanced Materials: Innovations like self-healing concrete to reduce lifecycle costs.
Expert Insights and Recommendations
Industry Quotes
"Companies that use technology as a resource to increase profitability as opposed to an expenditure will lead the construction industry in 2025." Dr. Sarah Chen, Construction Technology Institute.
“Cost optimization is aligning expenditures to value delivery, not reduction of expense.” Michael Ramirez, CFO National Construction Association.
Best Practices Shared by Successful Construction Companies
They are among the best practices which helped them get ahead of their competitors:
- Utilizing project analytics for opportunity identification.
- Collection of estimates: Enhance teamwork among estimating, operations, and finance disciplines.
- Client management: Create policies around pricing and terms with specific vendors.
- Internal training sessions: Ensure that teams are trained on new methods, processes, and relevant technologies.
- Client education: Teach clients how to appreciate the quality construction.
Conclusion
A more balanced approach is required by construction companies in managing costs and optimizing profits, as there are some areas in construction that could use cost-cutting while other functions require strategic investment. Construction companies are likely to improve their financial performance, both in the short and long-term, if they incorporate techniques discussed in this guide such as adopting innovative technologies, restructuring contracts, and maintaining quality service construction.
The leading construction companies in 2025 will be those that integrate their cost management into everyday practices as opposed to an isolated project. Construction firms can sustain profitability even when the market is tough, through systematic evaluation of business operations, integration of appropriate technology, and cultivating a culture of ongoing development.
FAQ
1. What’s the difference between cost reduction and cost optimization in construction?
Cost reduction is about cutting down on spending—like switching to cheaper materials or trimming services. Cost optimization, on the other hand, is about spending smarter—investing in better tools or systems that may cost more upfront but improve efficiency and returns in the long run.
2. Why is it important to balance cost-cutting with long-term investments in construction?
Focusing solely on cutting costs can hurt quality and efficiency. A balanced approach helps construction companies stay profitable in the short term while remaining competitive and resilient in the long term.
3. How can construction firms reduce project costs without compromising quality?
Using lean construction principles, standardizing procedures, and adopting prefabrication can help reduce waste. Investing in technologies like BIM and project management software can also lower rework and delays, improving overall cost-efficiency.
4. What role does technology play in cost reduction and profit growth?
Technology like drone surveys, automated equipment, and digital project tools reduces manual labor and errors, leading to lower costs. Construction firms that embrace digitalization typically see 15–20% cost savings compared to those that don’t.
5. How can construction companies maximize profits in 2025?
Strategic bidding, value-based pricing, and better contract clauses are key. Companies can also improve profits by training workers, using incentive programs, and analyzing past project performance for insights.
6. What are some real-world examples of cost and profit optimization in construction?
Horizon Builders saved $450,000 annually by tracking materials and reducing waste. Summit Contractors increased profit margins from 8% to 14% through value-based pricing. These examples show the financial impact of well-planned strategies.
7. What tools or technologies are recommended for better cost management in construction?
Tools like Procore, Buildertrend, and CoConstruct help with budgeting, planning, and team coordination. Advanced technologies like robotics, 3D printing, and modular construction are also changing the game by improving quality while reducing costs.